Automated Assembly
Gain a thorough understanding of Automated Assembly in manufacturing, with insights into their application, benefits, and strategic importance in the industry.
Overview of Automated Assembly
Automated Assembly is a sophisticated process involving the use of machinery and technology to assemble products with minimal human intervention. At its core, it aims to streamline manufacturing operations by integrating advanced technologies such as robotics, artificial intelligence (AI), and machine learning into production lines. This integration not only enhances productivity but also significantly reduces errors, improving overall product quality. In industries where precision and speed are paramount, such as automotive and electronics manufacturing, automated assembly plays a pivotal role in maintaining competitive advantage. By orchestrating complex sequences of tasks with high precision and speed, automated assembly facilitates high-volume production with consistent quality standards.
In the broader context of manufacturing, automated assembly serves as a critical component that interlinks with other processes such as supply chain management, inventory control, and quality assurance. For instance, in an automotive plant, automated assembly lines can be programmed to handle everything from welding car bodies to installing engines, all while communicating with inventory systems to ensure the right parts are available when needed. This level of integration not only improves operational efficiency but also enhances the ability to adapt to changes in production demands, thus providing a robust framework for modern manufacturing operations.
Role in Manufacturing Efficiency
The impact of automated assembly on manufacturing efficiency cannot be overstated. By significantly reducing cycle times and minimizing human error, automation allows manufacturers to achieve higher throughput in less time. This is particularly evident in industries that demand high precision and rapid production rates, such as electronics and automotive manufacturing. For example, companies like Tesla have leveraged automated assembly lines to drastically cut down the time it takes to produce a vehicle, thereby enabling them to meet growing consumer demand without compromising on quality.
Furthermore, automated assembly contributes to improved product quality by ensuring that each unit is assembled under consistent conditions, adhering to stringent quality standards. This consistency is achieved through the use of precision machinery and advanced monitoring systems that can detect and correct deviations in real-time. Industries such as pharmaceuticals, where compliance with health and safety regulations is critical, benefit immensely from the precision and accuracy provided by automated assembly systems.
The integration of automated assembly into manufacturing processes also facilitates lean manufacturing principles. By optimizing resource usage and minimizing waste, manufacturers can achieve greater cost-effectiveness and sustainability. This is increasingly important in today's manufacturing landscape, where there is a growing emphasis on reducing environmental impact and increasing the efficiency of resource use. Overall, automated assembly stands as a cornerstone in the quest for manufacturing excellence, driving efficiency, quality, and innovation.
Navigate Manufacturing Project Success with Meegle
Historical development of automated assembly
Origins of Automated Assembly
The journey of automated assembly can be traced back to the Industrial Revolution, a period that laid the groundwork for modern manufacturing through the introduction of mechanization. The initial steps towards automation involved the use of simple machines and mechanized processes to handle repetitive tasks, thereby increasing productivity and reducing labor costs. However, it wasn't until the advent of computer technology in the mid-20th century that the concept of automated assembly began to take a more defined shape.
One of the most significant milestones in the evolution of automated assembly was the introduction of programmable logic controllers (PLCs) in the 1960s. These devices allowed for greater flexibility and precision in controlling machinery, marking a shift from purely mechanical systems to those capable of complex, programmable tasks. This innovation paved the way for the development of automated assembly lines, which became a hallmark of industries such as automotive manufacturing. Companies like General Motors and Ford were pioneers in adopting these technologies, using them to revolutionize car production and set new benchmarks for efficiency and scale.
Evolution Over Time
As technology advanced, so too did the methodologies and capabilities of automated assembly systems. The introduction of robotic technology in the 1970s marked a new era of automation, allowing machines to perform tasks with a level of precision and reliability previously unattainable. Robotics enabled assembly lines to handle intricate tasks, such as electronic component assembly, with minimal human intervention. This evolution was fueled by innovations in computing and sensor technology, which provided the necessary tools for robots to operate with increased autonomy and sophistication.
The 21st century has seen further advancements with the integration of artificial intelligence and machine learning into automated assembly systems. These technologies enable machines to learn from data and improve their performance over time, leading to more efficient and adaptable manufacturing processes. The concept of the smart factory, where interconnected systems communicate and optimize operations autonomously, is a direct result of these advancements. Industries across the globe are leveraging these capabilities to enhance flexibility, reduce downtime, and increase overall production efficiency.
Through continuous innovation and adaptation, automated assembly has transformed from a simple mechanized process into a complex, intelligent system that drives modern manufacturing. As we move into the future, the potential for further advancements remains immense, with emerging technologies promising to push the boundaries of what is possible in automated assembly.
Click here to read our expertly curated top picks!
Core principles and techniques
Fundamental Concepts
Understanding the core principles of automated assembly is crucial for effectively implementing and optimizing these systems. At the heart of automated assembly lies the integration of robotics, artificial intelligence (AI), and system automation. Robotics involves the use of programmable machines capable of performing a range of tasks with high precision and speed. These machines are equipped with sensors and actuators that allow them to interact with their environment, making them indispensable in assembly processes that require handling delicate or complex parts.
AI integration further enhances the capabilities of automated assembly systems by enabling machines to learn from data and make informed decisions. Machine learning algorithms can analyze patterns in production data to optimize processes, reduce cycle times, and improve quality control. For example, in an electronics manufacturing plant, AI can be used to identify defects in real-time, allowing for immediate corrective actions and reducing waste.
System automation encompasses the orchestration of multiple machines and processes to work seamlessly together. This is achieved through the use of sophisticated software that coordinates tasks, manages resources, and ensures that production flows smoothly. Key terminologies in this domain include PLC programming, which involves creating instructions for machines to follow, and IoT integration, which allows devices to communicate and share data in real-time. Understanding these concepts is essential for implementing automated assembly systems that are efficient, reliable, and adaptable to changing production demands.
Implementation Techniques
The successful application of automated assembly requires a strategic approach to selecting and implementing the right techniques and technologies. Robotics forms the backbone of many automated assembly systems, and selecting the appropriate type of robot—whether it be a cobot (collaborative robot) or an industrial robot—depends on the specific requirements of the manufacturing process. Cobots, designed to work alongside humans, are ideal for tasks that require a high degree of flexibility and adaptability, while industrial robots are better suited for high-speed, repetitive tasks.
Machine learning and IoT are also critical components of modern automated assembly. Machine learning algorithms can be used to optimize assembly processes by analyzing production data and identifying areas for improvement. IoT devices, such as sensors and smart cameras, provide real-time data on production conditions, enabling proactive maintenance and reducing downtime. The choice of these techniques should be guided by the specific goals of the manufacturing operation, such as reducing waste, improving quality, or increasing throughput.
When implementing automated assembly, it is also important to consider the integration of these technologies with existing systems. This may involve upgrading legacy equipment, investing in new infrastructure, or retraining the workforce to manage and operate the new systems. A phased approach to implementation, starting with pilot projects and gradually scaling up, can help mitigate risks and ensure a smooth transition to automated assembly. By carefully selecting and implementing the right techniques, manufacturers can harness the full potential of automation to drive efficiency and innovation in their operations.
Benefits and challenges
Advantages in Production
The adoption of automated assembly in manufacturing offers a multitude of benefits that can significantly enhance production capabilities. One of the most notable advantages is the increase in efficiency, as automated systems can operate continuously without fatigue, leading to higher throughput and more consistent production rates. This is particularly beneficial in industries with high demand and tight deadlines, such as automotive and consumer electronics, where meeting production targets is critical to maintaining competitive advantage.
Another significant benefit is the reduction of human error, which is often a source of quality issues in manual assembly processes. Automated systems are programmed to perform tasks with a high degree of precision and consistency, ensuring that each product meets the required quality standards. This not only improves product quality but also reduces the cost associated with rework and returns, leading to greater overall cost savings.
Furthermore, automated assembly enables innovative manufacturing designs and processes that were previously unattainable. By leveraging advanced robotics and AI, manufacturers can create complex products with intricate designs more efficiently and at a lower cost. This opens up new possibilities for product innovation and customization, allowing manufacturers to cater to evolving consumer preferences and differentiate themselves in the market. Overall, the integration of automated assembly into production processes provides manufacturers with a powerful tool to enhance efficiency, quality, and competitiveness.
Potential Limitations
Despite its numerous advantages, the implementation of automated assembly is not without challenges. One of the primary obstacles is the high initial investment required to acquire and install the necessary equipment and technology. This can be a significant barrier for small and medium-sized enterprises (SMEs) with limited capital resources. Additionally, the integration of automated systems into existing production lines can be complex and time-consuming, requiring careful planning and execution to avoid disruptions.
Maintenance and upkeep of automated systems are also critical considerations, as these systems require regular servicing to operate optimally. The complexity of automated assembly equipment means that specialized skills and knowledge are often needed to perform maintenance and troubleshoot issues, which can lead to increased operational costs. Furthermore, there may be resistance from the workforce, who may feel threatened by the shift towards automation and the potential impact on their job roles.
To address these challenges, manufacturers can adopt a phased approach to implementation, starting with pilot projects to test the feasibility and impact of automation on their operations. Investing in workforce training and development is also crucial to ensure that employees are equipped with the skills needed to manage and operate automated systems. By fostering a culture of continuous improvement and embracing technological advancements, manufacturers can overcome these challenges and successfully integrate automated assembly into their production processes.
Click here to read our expertly curated top picks!
Case studies and real-world applications
Industry examples
Industry examples
Example 1: Automotive Manufacturing
In the automotive industry, automated assembly has been a game-changer, revolutionizing production lines and significantly enhancing speed and precision. Leading automotive manufacturers such as Toyota and BMW have integrated automated systems to streamline their assembly processes, allowing them to produce vehicles with greater efficiency and at a lower cost. The use of robotics in tasks such as welding, painting, and assembling complex components has not only reduced cycle times but also improved the overall quality and consistency of the final product. By embracing automation, these companies have been able to meet increasing consumer demands while maintaining high standards of quality and safety.
Example 2: Electronics Manufacturing
In the electronics sector, automated assembly plays a crucial role in achieving scalability and ensuring stringent quality control. Companies like Apple and Samsung have invested heavily in automated systems to produce their consumer electronics with high precision and speed. Automated pick-and-place machines, for example, are used to accurately position tiny components onto circuit boards, ensuring that each device functions as intended. The integration of AI and machine learning into these systems further enhances their capabilities, enabling real-time defect detection and process optimization. As a result, electronics manufacturers can meet the growing demand for high-quality devices while reducing production costs and time-to-market.
Example 3: Pharmaceutical Manufacturing
In the pharmaceutical industry, automated assembly is instrumental in ensuring accuracy and compliance with stringent regulatory standards. The production of medications requires precise handling and measurement of ingredients, which can be efficiently managed through automated systems. Pharmaceutical companies such as Pfizer and Novartis have implemented automation in their production lines to improve accuracy, reduce contamination risks, and increase production capacity. Automated systems also facilitate data collection and analysis, providing valuable insights into process performance and enabling continuous improvement. By leveraging automated assembly, pharmaceutical manufacturers can ensure the safety and efficacy of their products while enhancing operational efficiency.
Impact analysis
Impact analysis
The implementation of automated assembly across various sectors has led to tangible improvements in efficiency, quality, and competitiveness. Key performance indicators (KPIs) such as cycle time, defect rates, and overall equipment effectiveness (OEE) are commonly used to measure the success of automation initiatives. In the automotive industry, for example, companies have reported significant reductions in production time and improvements in product quality, leading to higher customer satisfaction and increased market share. Similarly, in the electronics sector, the ability to achieve higher precision and consistency has resulted in fewer product defects and recalls, ultimately enhancing brand reputation and profitability.
In the pharmaceutical industry, the adoption of automated assembly has led to increased production capacity and improved compliance with regulatory requirements, reducing the risk of costly fines and recalls. The ability to produce high-quality products at scale also provides a competitive advantage in a market where consumer trust and safety are paramount. Overall, the impact of automated assembly on manufacturing is profound, driving improvements across key performance metrics and enabling companies to achieve greater success in their respective industries.
Technological integration and innovations
Current Technologies
The integration of current technologies such as robotics, AI, and the Internet of Things (IoT) has significantly enhanced the capabilities of automated assembly systems. Robotics, with its ability to perform precise and repetitive tasks, forms the foundation of many automated assembly processes. Advanced robotic systems equipped with sensors and machine vision can adapt to changes in the production environment, making them highly versatile and efficient.
AI and machine learning further enhance the capabilities of automated assembly by enabling systems to learn from data and improve their performance over time. For example, AI algorithms can analyze production data to identify patterns and anomalies, allowing for predictive maintenance and real-time process optimization. This not only reduces downtime but also enhances the overall efficiency and reliability of the production process.
The integration of IoT devices into automated assembly systems provides real-time data on production conditions, enabling manufacturers to monitor and control processes remotely. IoT devices can communicate with each other and with central control systems, allowing for seamless coordination and optimization of production activities. This level of connectivity and data exchange is essential for creating more efficient and adaptable manufacturing systems, ultimately leading to improved productivity and competitiveness.
Future Trends
Looking ahead, the future of automated assembly is poised for exciting developments and innovations. Emerging trends such as smart factories and digital twins are set to redefine manufacturing practices, offering new opportunities for efficiency and flexibility. Smart factories leverage advanced technologies such as AI, IoT, and big data analytics to create interconnected and autonomous production environments. This enables manufacturers to optimize operations in real-time, respond quickly to changes in demand, and reduce waste, ultimately enhancing overall efficiency and sustainability.
Digital twins, virtual replicas of physical systems, allow manufacturers to simulate and analyze production processes in a virtual environment. This provides valuable insights into how systems will perform under different conditions, enabling manufacturers to optimize processes and reduce the risk of costly errors. As digital twin technology continues to evolve, it is expected to play an increasingly important role in automated assembly, providing manufacturers with powerful tools for innovation and continuous improvement.
Overall, the future of automated assembly is bright, with advancements in technology promising to push the boundaries of what is possible in manufacturing. By staying abreast of these trends and embracing new innovations, manufacturers can position themselves for success in an increasingly competitive and dynamic market.
Click here to read our expertly curated top picks!
Tips for successful automated assembly implementation
Do's | Don'ts |
---|---|
Conduct thorough research and planning before implementation. | Avoid rushing the integration process without adequate preparation. |
Invest in workforce training to ensure a smooth transition. | Don't neglect the importance of regular maintenance and updates. |
Embrace technological advancements and stay adaptable. | Don't resist change or overlook emerging technologies. |
Click here to read our expertly curated top picks!
Conclusion
Summary of Key Points
Automated Assembly represents a significant advancement in manufacturing, offering numerous benefits such as increased efficiency, reduced human error, and improved product quality. By leveraging advanced technologies such as robotics, AI, and IoT, manufacturers can create more streamlined and adaptable production processes. The historical development of automated assembly highlights its evolution from simple mechanized processes to complex, intelligent systems that drive innovation and competitiveness.
Encouraging Ongoing Adaptation
As the manufacturing landscape continues to evolve, it is crucial for industry professionals to stay updated on technological advancements and consider integrating automated assembly into their strategies. By embracing automation and fostering a culture of continuous improvement, manufacturers can position themselves for success in an increasingly competitive and dynamic market. The future of automated assembly holds immense potential, and those who adapt and innovate will be well-equipped to thrive in this new era of manufacturing.
Navigate Manufacturing Project Success with Meegle
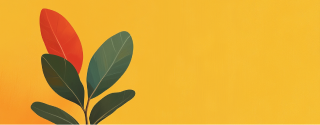
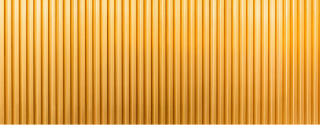
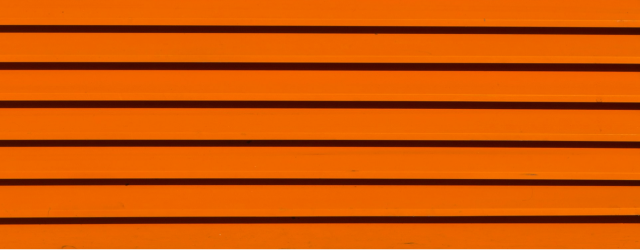
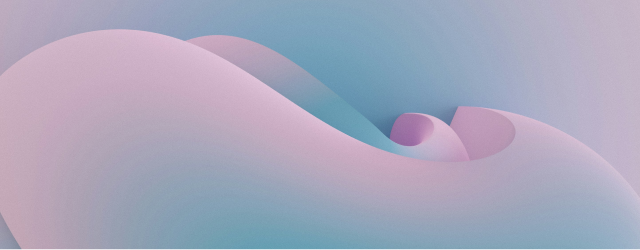
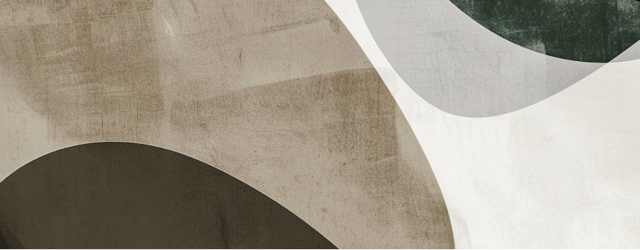
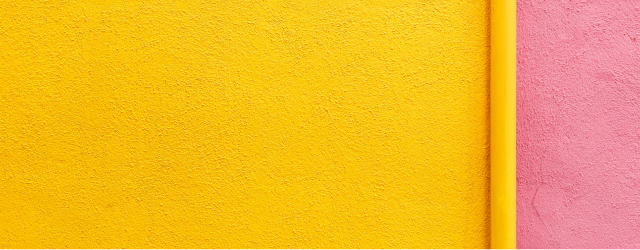
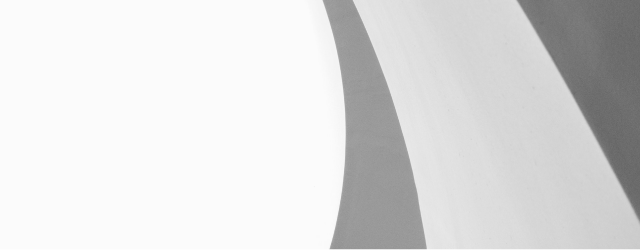
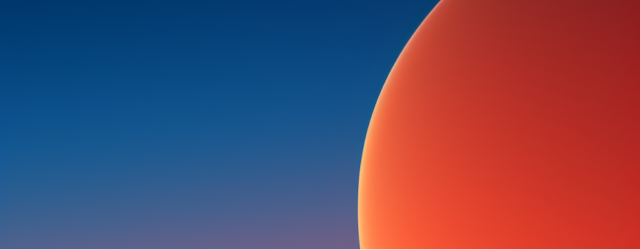