Automated Guided Vehicles (AGV)
Gain a thorough understanding of Automated Guided Vehicles (AGV) in manufacturing, with insights into their application, benefits, and strategic importance in the industry.
Overview of Automated Guided Vehicles (AGV)
Automated Guided Vehicles (AGVs) are at the heart of modern automated material handling systems, offering a streamlined approach to managing logistics within manufacturing environments. These autonomous vehicles are designed to move materials across factory floors without human intervention, relying on technologies such as magnetic strips, lasers, or vision systems for navigation. The core advantage of AGVs lies in their ability to perform repetitive and mundane tasks, freeing up human workers for more complex duties. This automation not only reduces labor costs but significantly enhances manufacturing throughput, making AGVs indispensable in high-volume production settings.
AGVs come in various forms, including tow vehicles, unit load carriers, and forklift types, each tailored to specific operational needs. They are equipped with sophisticated sensors and control systems that enable precise movement and obstacle detection, ensuring safety and efficiency. The integration of AGVs into manufacturing processes allows companies to achieve higher levels of consistency, speed, and accuracy in material transport, ultimately leading to improved product quality and customer satisfaction.
Role in Manufacturing Efficiency
The deployment of AGVs in manufacturing settings plays a crucial role in boosting efficiency and productivity. By automating the transport of materials, AGVs ensure timely delivery to production lines, reducing bottlenecks and delays. This efficiency is further enhanced when AGVs are integrated with Warehouse Management Systems (WMS) and Enterprise Resource Planning (ERP) systems, allowing for seamless coordination of tasks and optimization of inventory management. Such integration helps in reducing human errors, which are often a source of costly mistakes and downtime.
Moreover, AGVs contribute to a safer work environment by minimizing human-vehicle interactions, which can lead to accidents. Their ability to navigate complex factory layouts ensures that materials are delivered precisely where they are needed, reducing the risk of damage or loss. In environments where precision and timing are critical, such as just-in-time production systems, AGVs are invaluable in maintaining continuous flow and ensuring that production schedules are adhered to.
The impact of AGVs on manufacturing efficiency is evidenced by their ability to adapt to various production needs. Whether it’s moving raw materials to processing areas or delivering finished goods to storage, AGVs can be programmed to perform these tasks with minimal supervision. The result is a more agile and responsive manufacturing operation that can quickly adjust to changes in demand or production schedules, ultimately leading to increased competitiveness in the market.
Navigate Manufacturing Project Success with Meegle
Historical development of automated guided vehicles (agv)
Origins of Automated Guided Vehicles (AGV)
The concept of Automated Guided Vehicles (AGVs) dates back to the 1950s, when the first mechanized carts were introduced to automate material handling in warehouses. These early systems were rudimentary, utilizing wire-guided navigation to move along pre-defined paths. Despite their simplicity, they marked a significant milestone in the journey towards automation, laying the groundwork for the advanced systems we see today. Initially, AGVs were primarily used for transporting goods in storage facilities, reducing the need for manual labor and increasing operational efficiency.
Over the years, the application of AGVs expanded beyond warehouses to include manufacturing environments. Their ability to handle increased loads with precision made them invaluable in sectors like automotive and electronics, where efficient material transport is critical to production success. These early AGVs were limited in their capabilities, but they showcased the potential of automated systems to transform industrial operations, prompting further research and development.
Evolution Over Time
The evolution of AGVs has been driven by advancements in technology, particularly in sensor systems and software algorithms. From wire-guided systems, AGVs progressed to more sophisticated laser and vision-guided technologies, allowing for increased flexibility and adaptability in various environments. The introduction of RFID tags and QR codes enhanced navigation precision, enabling AGVs to operate in more complex settings with dynamic changes.
One of the most significant advancements in AGV technology is the development of Simultaneous Localization and Mapping (SLAM). This technique allows AGVs to build and update maps of their surroundings while keeping track of their location, offering better navigation in unpredictable environments. With SLAM, AGVs can adjust their paths in real-time to avoid obstacles, making them more efficient and safer.
Furthermore, the integration of machine learning and artificial intelligence has led to smarter AGVs that can analyze data and optimize their operations autonomously. These advancements have broadened the scope of applications for AGVs, from simple transportation tasks to more complex roles like assembly and quality inspection. The continuous evolution of AGVs reflects the growing demand for automation in manufacturing, driving innovation and pushing the boundaries of what these vehicles can achieve.
Click here to read our expertly curated top picks!
Core principles and techniques
Fundamental Concepts
Automated Guided Vehicles (AGVs) operate based on several fundamental principles that define their functionality and efficiency. Understanding these core concepts is essential for implementing AGV systems effectively within a manufacturing environment. One of the primary principles is path planning, which involves designing optimal routes for AGVs to follow, ensuring timely and efficient material transport. Path planning takes into account various factors such as distance, obstacles, and production schedules to minimize travel time and maximize throughput.
Another crucial concept is obstacle avoidance, which is critical for maintaining safety and preventing collisions. AGVs are equipped with sensors and algorithms that enable them to detect and maneuver around obstacles in real-time. This capability is particularly important in crowded factory floors where unexpected changes can occur, ensuring that AGVs can operate without human intervention.
Energy management is also a key principle of AGV operation, focusing on optimizing battery usage and minimizing downtime. AGVs are designed to monitor their energy levels and return to charging stations as needed, ensuring continuous operation and reducing the risk of production delays. Efficient energy management contributes to the sustainability of AGV systems by prolonging battery life and reducing overall energy consumption.
Implementation Techniques
Implementing AGVs in a manufacturing environment requires meticulous planning and execution, involving several techniques to ensure success. One of the first steps is defining pathways and designing layouts that accommodate AGV movement without disrupting existing processes. This involves mapping out routes that align with production goals and considering factors such as speed, efficiency, and safety.
Integration with existing systems is another crucial aspect of AGV implementation. AGVs must be compatible with Warehouse Management Systems (WMS) and Enterprise Resource Planning (ERP) systems to facilitate seamless communication and coordination. This integration allows for real-time data exchange, enabling AGVs to respond to changes in production schedules and inventory levels dynamically.
Customization of AGVs for specific tasks is also an important technique, ensuring that the vehicles are equipped with the necessary tools and capabilities to perform their intended roles. This may involve selecting the appropriate type of AGV, such as unit load carriers or tow vehicles, and configuring them with the necessary sensors and software to handle particular materials or navigate specific environments.
The use of mapping technologies like SLAM is essential for deploying AGVs in dynamic environments. SLAM enables AGVs to build and update maps of their surroundings, allowing them to navigate complex factory layouts with precision. By leveraging SLAM, businesses can ensure that AGVs operate effectively even in unpredictable settings, reducing the risk of errors and enhancing overall productivity.
Benefits and challenges
Advantages in Production
The implementation of Automated Guided Vehicles (AGVs) in manufacturing offers numerous advantages that significantly enhance production efficiency and operational effectiveness. One of the most notable benefits is the reduction in operational costs. By automating material transport, AGVs minimize the need for manual labor, leading to substantial savings in labor expenses. Additionally, AGVs improve safety by reducing human-vehicle interactions, which can lead to accidents and injuries. Their ability to operate autonomously ensures that materials are moved safely and accurately, minimizing the risk of damage or loss.
AGVs also provide flexibility in manufacturing layouts, allowing businesses to adapt to changing production needs without major disruptions. Their ability to navigate complex environments means that they can be easily reconfigured to accommodate new processes or products, supporting agile manufacturing strategies. This flexibility is particularly valuable in industries where production demands can fluctuate, enabling companies to respond quickly to market changes.
Furthermore, AGVs contribute to sustainability by optimizing energy use and reducing waste. Their efficient energy management systems ensure minimal power consumption, while precise material handling reduces the likelihood of damage or spoilage. This not only supports environmental goals but also enhances the overall efficiency of manufacturing operations.
Potential Limitations
Despite their significant benefits, AGVs also face challenges that can impact their implementation and effectiveness in manufacturing environments. One of the primary challenges is the high initial investment cost. The deployment of AGVs involves substantial financial outlay for the acquisition of vehicles, installation of infrastructure, and integration with existing systems. This can be a barrier for smaller companies or those with limited budgets.
Another challenge is the complexity involved in deploying AGVs, particularly in environments with legacy systems. Integrating AGVs with outdated technology can lead to compatibility issues and require additional resources to resolve. This complexity can extend the implementation timeline and increase costs, making it crucial for businesses to carefully plan and coordinate their efforts.
The dynamic nature of manufacturing environments can also pose challenges for AGVs, as they must adapt to changes in production processes and layouts. This requires ongoing monitoring and optimization to ensure that AGVs operate efficiently and effectively. Leveraging advancements in IoT and AI can help address these challenges, providing real-time data analytics and predictive maintenance capabilities to enhance AGV performance.
Click here to read our expertly curated top picks!
Case studies and real-world applications
Industry examples
Industry examples
-
Automotive Manufacturing: Companies like Tesla have embraced Automated Guided Vehicles (AGVs) to streamline their production processes. Tesla uses AGVs to transport heavy vehicle parts across their assembly lines, reducing the time required for manual material handling and speeding up assembly. The implementation of AGVs has allowed Tesla to enhance its production efficiency, reduce labor costs, and improve overall throughput, contributing to its competitive edge in the automotive industry.
-
Pharmaceuticals: In the pharmaceutical sector, firms like Pfizer utilize AGVs to move sensitive materials within their manufacturing facilities. The precision and reliability of AGVs ensure that materials are transported safely, adhering to stringent safety and compliance regulations. By automating material handling, Pfizer can minimize human error and contamination risks, ensuring the quality and integrity of their products. The use of AGVs has led to increased productivity and compliance, supporting Pfizer's commitment to delivering safe and effective pharmaceuticals.
-
Food and Beverage: Coca-Cola has implemented AGVs in their packaging and palletizing operations, enhancing production speed and accuracy. AGVs are used to transport materials and finished products efficiently, reducing manual handling and optimizing workflow. This automation has allowed Coca-Cola to increase production capacity, maintain high-quality standards, and reduce operational costs. The integration of AGVs into their processes exemplifies the transformative impact of automation in the food and beverage industry.
Impact analysis
Impact analysis
The adoption of Automated Guided Vehicles (AGVs) in these sectors has led to measurable improvements that underscore their transformative potential in industrial settings. One of the most significant impacts is the reduction in labor costs, as AGVs take over repetitive and time-consuming tasks, freeing up human workers for more strategic roles. This shift not only leads to cost savings but also enhances workforce satisfaction and productivity.
Another notable impact is the increase in manufacturing throughput, with AGVs enabling faster and more efficient material transport. This improvement in speed and accuracy contributes to higher production volumes, supporting companies in meeting market demands and achieving competitive advantages. The precise navigation and handling capabilities of AGVs ensure that materials are delivered exactly where they are needed, reducing delays and errors.
Enhanced safety standards are also a key outcome of AGV adoption, as the automation of material handling minimizes the risk of accidents and injuries. This improvement in safety not only protects workers but also reduces liability and compliance costs for businesses. Overall, the implementation of AGVs in various sectors highlights their ability to drive operational excellence and sustainability, paving the way for future advancements in automation technology.
Technological integration and innovations
Current Technologies
Automated Guided Vehicles (AGVs) leverage a range of advanced technologies to optimize their operations and enhance their capabilities. Artificial intelligence and machine learning play a significant role in enabling AGVs to analyze data and make autonomous decisions, improving their efficiency and adaptability. These technologies allow AGVs to learn from their surroundings, optimize their paths, and respond to changes in real-time, ensuring seamless operation in dynamic environments.
The integration of Internet of Things (IoT) technology further enhances AGV functionality, providing real-time data analytics and predictive maintenance capabilities. IoT sensors enable AGVs to monitor their performance, detect anomalies, and anticipate maintenance needs, reducing downtime and ensuring continuous operation. This connectivity also allows AGVs to communicate with other automated systems, facilitating coordinated workflows and optimizing overall production processes.
Moreover, navigation technologies such as lasers, vision systems, and SLAM are crucial for AGV operation, enabling precise movement and obstacle detection. These technologies allow AGVs to navigate complex factory layouts with accuracy, ensuring that materials are delivered safely and efficiently. The combination of these cutting-edge technologies empowers AGVs to perform a wide range of tasks, from simple transport to complex assembly and inspection roles.
Future Trends
The future of Automated Guided Vehicles (AGVs) promises exciting advancements that will further enhance their efficiency and sustainability in manufacturing processes. One of the key trends is the development of autonomous navigation systems, allowing AGVs to operate independently without pre-defined paths. These systems leverage AI and machine learning to adapt to changes in real-time, optimizing routes and improving operational flexibility.
Enhanced interoperability with smart factories is another emerging trend, with AGVs integrating seamlessly into Industry 4.0 ecosystems. This connectivity enables AGVs to collaborate with other automated systems, facilitating coordinated and efficient workflows. The use of IoT and cloud computing will further enhance data exchange and analytics, allowing for more strategic decision-making and optimization.
The increased use of renewable energy sources is also a promising trend, as manufacturers seek to enhance sustainability and reduce environmental impact. AGVs equipped with solar panels or energy-efficient batteries can operate with minimal power consumption, supporting green manufacturing initiatives. These advancements will contribute to the overall efficiency and eco-friendliness of AGV systems, aligning with global sustainability goals.
Click here to read our expertly curated top picks!
Tips for do's and don'ts of agv implementation
Do's | Don'ts |
---|---|
Conduct a thorough needs analysis. | Rush the implementation process. |
Involve cross-functional teams. | Ignore staff training requirements. |
Leverage technology for integration. | Overlook safety compliance. |
Plan for future scalability. | Neglect continuous improvement. |
Click here to read our expertly curated top picks!
Conclusion
Summary of Key Points
In conclusion, Automated Guided Vehicles (AGVs) are pivotal in modernizing manufacturing processes, offering numerous benefits like operational efficiency, cost reduction, and enhanced safety. Their continued evolution and integration with new technologies will further expand their applicability and impact, driving industrial innovation and competitiveness.
Encouraging Ongoing Adaptation
As AGVs continue to evolve, it is crucial for industry professionals to stay informed and consider their strategic implementation. Embracing AGVs not only enhances current manufacturing capabilities but also positions companies at the forefront of industrial innovation. Adopting AGVs is a step towards a more efficient, sustainable, and competitive manufacturing future, underscoring the importance of adapting to technological advancements in today's fast-paced industrial landscape.
Navigate Manufacturing Project Success with Meegle
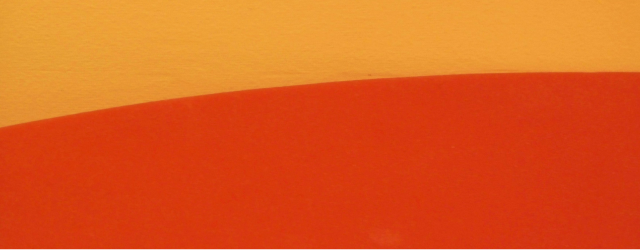
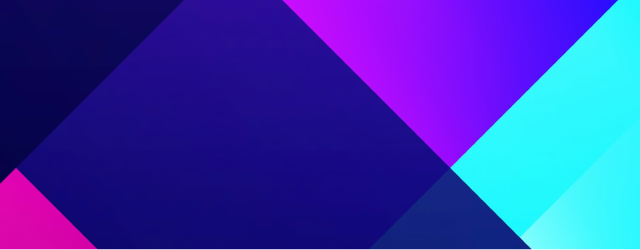
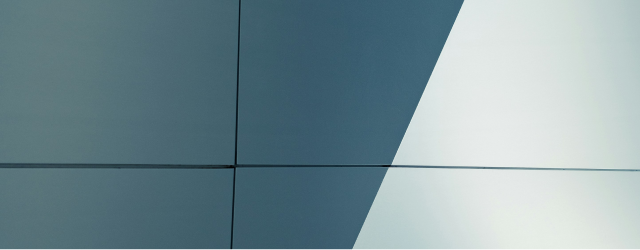
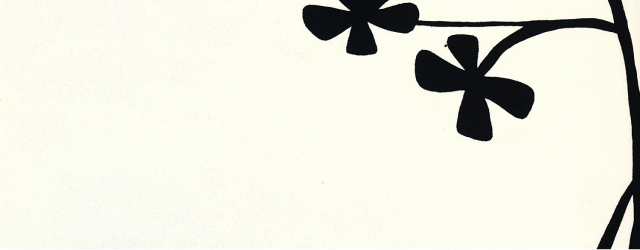
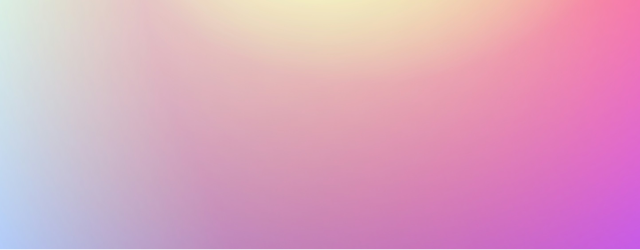
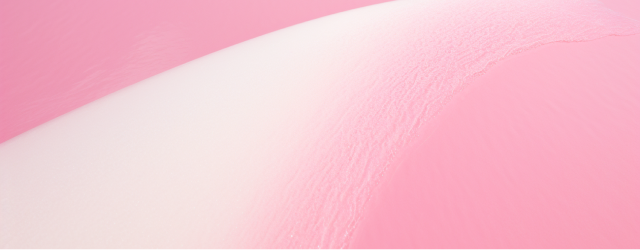
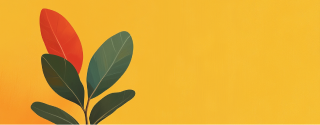
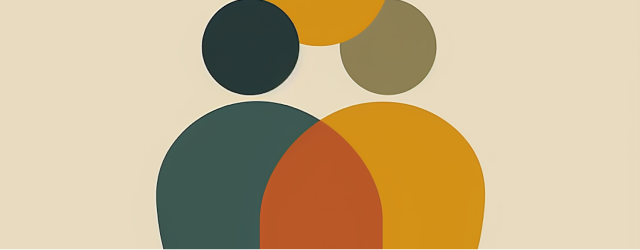