Automation Systems
Gain a thorough understanding of Automation Systems in manufacturing, with insights into their application, benefits, and strategic importance in the industry.
Overview of Automation Systems
Automation systems in manufacturing refer to the use of technology to control and monitor production processes, minimizing human intervention and optimizing operations. These systems consist of several core components: sensors, controllers, actuators, and software interfaces. Sensors gather data from the manufacturing environment, controllers process this data to make decisions, and actuators execute these decisions by performing specific tasks. Software interfaces facilitate communication between these components, enabling seamless operation.
The integration of automation systems in manufacturing is a game-changer. By streamlining operations, these systems enhance efficiency and ensure consistent product quality. They offer a holistic approach, connecting various aspects of the manufacturing process to create a more efficient workflow. This integration reduces the need for manual labor, minimizes errors, and increases the speed of production.
Moreover, automation systems empower manufacturers to adapt quickly to changing demands, such as shifts in consumer preferences or supply chain disruptions. By automating routine tasks, manufacturers can allocate human resources to more strategic activities, such as product development and innovation. This shift not only improves operational efficiency but also positions manufacturers to respond effectively to market challenges and opportunities.
Role in Manufacturing Efficiency
Automation systems play a critical role in enhancing manufacturing efficiency. They reduce cycle times by automating repetitive tasks, thereby increasing throughput and enabling faster production. By minimizing human error, automation systems ensure precision and consistency in product quality, which is crucial for maintaining brand reputation and customer satisfaction.
Resource utilization is another area where automation systems excel. By optimizing processes, these systems reduce waste and energy consumption, contributing to cost savings and environmental sustainability. Automation systems also facilitate real-time monitoring and adaptive control, allowing manufacturers to proactively address issues before they impact production.
The ability to conduct predictive maintenance is a significant advantage of automation systems. By continuously monitoring equipment performance, manufacturers can anticipate maintenance needs and avoid unexpected downtime. This proactive approach not only extends the lifespan of machinery but also ensures uninterrupted production, further enhancing efficiency.
In essence, automation systems transform manufacturing operations, making them more agile and responsive. As a result, manufacturers can achieve higher productivity levels, improve product quality, and reduce operational costs, all of which are essential for maintaining competitiveness in the industry.
Navigate Manufacturing Project Success with Meegle
Historical development of automation systems
Origins of Automation Systems
The origins of automation systems can be traced back to the Industrial Revolution, a period marked by significant technological advancements that laid the foundation for modern manufacturing. During this era, mechanization began to replace manual labor, leading to increased productivity and efficiency. The development of steam power and the mechanized loom are prime examples of early automation efforts.
As manufacturing evolved, the introduction of programmable logic controllers (PLCs) marked a pivotal moment in automation history. PLCs revolutionized process control, allowing manufacturers to automate complex tasks with precision and reliability. This innovation paved the way for the widespread adoption of automation systems across various industries.
The rise of robotics in manufacturing further accelerated the transition to automation. Robots introduced unprecedented levels of efficiency and precision, performing tasks that were previously impossible or impractical for human workers. This advancement not only improved production capabilities but also expanded the scope of automation, enabling manufacturers to explore new possibilities.
Throughout history, automation systems have continually evolved, driven by technological advancements and changing industry demands. From the early mechanical systems to sophisticated computer-controlled machinery, automation has become an integral part of manufacturing, shaping how products are made and delivered to consumers.
Evolution Over Time
The evolution of automation systems has been characterized by technological advancements that have transformed them into flexible, adaptive solutions capable of handling diverse manufacturing tasks. Initially, automation systems were rigid and limited in scope, designed to perform specific functions without the ability to adapt to changing conditions.
The integration of artificial intelligence (AI), the Internet of Things (IoT), and machine learning has revolutionized automation systems, making them more intelligent and interconnected. These technologies enable automation systems to learn from data, make decisions, and optimize processes autonomously. As a result, manufacturers can achieve greater efficiency, reduce costs, and improve product quality.
The shift from rigid automation to flexible systems has allowed manufacturers to respond more effectively to changing market demands. For example, the implementation of AI-driven robotics has enabled manufacturers to perform complex tasks with precision and adaptability, such as assembly line adjustments and custom product configurations.
Moreover, the advent of IoT has facilitated real-time monitoring and control, allowing manufacturers to gather and analyze data from connected devices. This capability enhances decision-making, enabling manufacturers to optimize operations and improve efficiency. Machine learning algorithms further refine this process, providing insights that drive continuous improvement.
The evolution of automation systems is ongoing, with new technologies continually emerging to enhance capabilities and expand possibilities. As manufacturers embrace these advancements, they can leverage automation systems to achieve greater flexibility, adaptability, and innovation in their operations.
Click here to read our expertly curated top picks!
Core principles and techniques
Fundamental Concepts
To understand automation systems in manufacturing, it is essential to grasp the fundamental concepts that underpin their design and operation. At the heart of these systems are control systems, feedback loops, and data acquisition, which together form the basis for effective automation.
Control systems are responsible for managing the operation of automation systems, ensuring that tasks are performed accurately and efficiently. They include hardware and software components that work together to control processes, such as regulating temperature, pressure, and flow in manufacturing environments.
Feedback loops are critical to maintaining system stability and performance. By continuously monitoring outputs and adjusting inputs, feedback loops enable automation systems to correct deviations and optimize processes. This capability ensures consistent product quality and reduces the need for manual intervention.
Data acquisition is the process of collecting and analyzing data from sensors and other sources to inform decision-making. Automation systems rely on data to monitor operations, identify trends, and optimize performance. By leveraging data, manufacturers can gain insights into their processes, enabling them to make informed decisions and drive continuous improvement.
Understanding these fundamental concepts is crucial for designing and operating effective automation systems. By applying these principles, manufacturers can create systems that are reliable, efficient, and capable of adapting to changing conditions.
Implementation Techniques
Implementing automation systems in manufacturing requires a strategic approach that considers process mapping, systems integration, and simulation modeling. These techniques are essential for designing and deploying automation systems that deliver maximum benefits while minimizing risks.
Process mapping involves analyzing and documenting existing workflows to identify opportunities for automation. By understanding the current state of operations, manufacturers can pinpoint areas where automation can enhance efficiency and reduce costs. This technique is crucial for ensuring that automation solutions are aligned with business objectives.
Systems integration is the process of connecting automation components to create a cohesive system. It involves integrating hardware, software, and communication networks to enable seamless operation. Systems integration is essential for ensuring that automation systems work together effectively, delivering consistent performance and reliability.
Simulation modeling is a powerful tool for testing and optimizing automation systems before deployment. By simulating real-world conditions, manufacturers can identify potential issues, optimize performance, and validate system designs. This technique reduces the risk of costly errors and ensures that automation systems deliver the desired outcomes.
To successfully implement automation systems, manufacturers must also consider risk assessment and scalability. By evaluating potential risks and designing systems that can scale with business growth, manufacturers can ensure long-term success and adaptability.
Benefits and challenges
Advantages in Production
Automation systems offer numerous advantages in manufacturing, including increased throughput, improved safety, and enhanced flexibility. These benefits are crucial for achieving competitive advantage and driving innovation in product development.
Increased throughput is one of the most significant advantages of automation systems. By automating repetitive tasks, manufacturers can achieve faster production rates, reducing cycle times and increasing output. This capability is essential for meeting market demands and improving profitability.
Improved safety is another critical benefit of automation systems. By reducing the need for human intervention in hazardous tasks, automation systems minimize the risk of accidents and injuries. This improvement not only protects workers but also enhances operational efficiency, as fewer workplace incidents lead to reduced downtime and associated costs.
Enhanced flexibility is a key advantage of automation systems, allowing manufacturers to adapt quickly to changing market conditions. Automation systems enable manufacturers to configure production lines to accommodate new products, variations, and customizations. This flexibility is essential for responding to consumer demands and exploring new market opportunities.
Moreover, automation systems facilitate faster time-to-market for new products. By streamlining processes and reducing development cycles, manufacturers can bring innovative products to market more quickly, gaining a competitive edge and satisfying customer needs.
Potential Limitations
Despite their advantages, automation systems pose several challenges, including high initial investment, complexity of integration, and workforce adaptation. Addressing these challenges is crucial for realizing the full potential of automation systems in manufacturing.
High initial investment is one of the primary barriers to automation adoption. The cost of equipment, software, and installation can be substantial, requiring careful financial planning and justification. However, phased implementation and strategic investment can mitigate this challenge, allowing manufacturers to realize returns over time.
The complexity of integration is another challenge, as manufacturers must connect diverse components and systems to create a cohesive automation solution. This process requires specialized expertise and careful planning to ensure compatibility and performance. Manufacturers can overcome this challenge by collaborating with experienced vendors and leveraging proven integration techniques.
Workforce adaptation is a critical challenge, as automation systems can disrupt traditional roles and processes. To address this issue, manufacturers must invest in training programs and clear communication to help employees understand and embrace automation. By showcasing the benefits and opportunities associated with automation, manufacturers can foster a positive transition and minimize resistance.
Strategic planning is essential for overcoming these challenges and maximizing the benefits of automation systems. By adopting a phased approach, engaging stakeholders, and prioritizing workforce development, manufacturers can successfully integrate automation systems and achieve long-term success.
Click here to read our expertly curated top picks!
Case studies and real-world applications
Industry examples
Industry examples
In the automotive industry, automation systems have become indispensable for enhancing production efficiency and quality. A prime example is Toyota's implementation of automation systems in their manufacturing plants. By integrating robotics and AI-driven systems, Toyota has achieved significant improvements in production speed and quality consistency. The automation systems allow for precise assembly and automated inspections, drastically reducing the margin for error and ensuring high standards of quality.
The electronics industry also showcases successful automation implementation. Samsung, for instance, uses advanced automation systems in their semiconductor fabrication plants. These systems incorporate real-time data analytics and machine learning, optimizing every stage of production from wafer fabrication to chip assembly. The result is enhanced throughput, reduced waste, and improved product reliability. Samsung's automation strategy exemplifies how comprehensive system integration can lead to superior performance and market leadership.
In the food production sector, automation systems have revolutionized operations. Nestle, a global food giant, has embraced automation to enhance their processing and packaging lines. With the integration of IoT and robotics, Nestle has achieved streamlined operations that minimize human intervention, ensuring consistency and safety. The automated systems allow for precise ingredient measurements, efficient packaging, and real-time monitoring of production lines, resulting in improved product quality and reduced costs.
These industry examples underscore the transformative potential of automation systems. By leveraging advanced technologies and strategic implementation, manufacturers across various sectors can achieve remarkable improvements in efficiency, quality, and competitiveness.
Impact analysis
Impact analysis
The impact of automation systems in manufacturing is profound, affecting productivity, quality, and cost-efficiency. A comprehensive analysis reveals how automation systems have reshaped industry practices and outcomes.
In terms of productivity, automation systems have enabled manufacturers to achieve unprecedented levels of throughput. By automating repetitive tasks and optimizing workflows, manufacturers can produce more goods in less time, significantly enhancing operational efficiency. This increase in productivity not only supports growth but also positions manufacturers to meet rising market demands.
Automation systems have also had a significant impact on product quality. The precision and consistency offered by automated processes ensure that products meet stringent quality standards. This improvement reduces the incidence of defects and enhances customer satisfaction, contributing to brand reputation and loyalty.
Cost-efficiency is another major impact of automation systems. By optimizing resource utilization and reducing waste, manufacturers can achieve substantial cost savings. Automated systems also facilitate predictive maintenance, minimizing downtime and associated costs. These efficiencies translate into improved profitability and competitiveness, enabling manufacturers to invest in innovation and expansion.
Technological integration and innovations
Current Technologies
The integration of current technologies such as AI, IoT, and cloud computing has significantly enhanced automation systems in manufacturing. These technologies contribute to creating intelligent and interconnected manufacturing environments, revolutionizing industry practices.
Artificial Intelligence (AI) plays a pivotal role in automation systems by enabling machines to learn from data and make decisions autonomously. AI algorithms analyze vast amounts of data to optimize processes, improve efficiency, and reduce waste. In manufacturing, AI-driven systems can predict equipment failures, recommend maintenance actions, and adjust production schedules based on real-time data.
The Internet of Things (IoT) facilitates seamless connectivity between devices and systems, enabling real-time monitoring and control. IoT sensors collect data from various points in the manufacturing process, providing valuable insights into operations. This connectivity allows manufacturers to optimize workflows, enhance decision-making, and improve overall efficiency.
Cloud computing offers scalable and flexible solutions for managing automation systems. By leveraging cloud platforms, manufacturers can store and process large volumes of data, enabling advanced analytics and machine learning applications. Cloud computing also supports remote monitoring and control, allowing manufacturers to manage operations from anywhere.
The integration of these technologies creates a dynamic manufacturing environment where systems are intelligent, adaptable, and responsive. By harnessing AI, IoT, and cloud computing, manufacturers can achieve greater efficiency, flexibility, and innovation, positioning themselves for sustained success.
Future Trends
The future of automation systems is marked by exciting trends that promise to further transform manufacturing strategies. Advancements in AI-driven automation, collaborative robots, and edge computing are set to revolutionize industry practices.
AI-driven automation will continue to evolve, enabling more sophisticated decision-making and optimization capabilities. As AI algorithms become more advanced, automation systems will be able to predict market trends, optimize supply chains, and personalize production processes. This trend promises to enhance flexibility and responsiveness, allowing manufacturers to adapt quickly to changing demands.
Collaborative robots, or cobots, represent another significant trend. Unlike traditional robots, cobots are designed to work alongside human workers, enhancing productivity and safety. Cobots can perform complex tasks and interact with humans in real-time, creating a more efficient and adaptable manufacturing environment. As cobots become more prevalent, manufacturers will be able to achieve greater efficiency and flexibility in their operations.
Edge computing is poised to transform automation systems by enabling faster data processing and decision-making at the edge of the network. This technology reduces latency and enhances real-time capabilities, allowing manufacturers to optimize processes and respond to changes instantly. Edge computing supports advanced analytics and machine learning, providing valuable insights into operations and driving continuous improvement.
As these trends unfold, manufacturers must stay abreast of technological advancements and consider their strategic implications. By embracing AI-driven automation, collaborative robots, and edge computing, manufacturers can enhance their competitiveness and drive innovation in their operations.
Click here to read our expertly curated top picks!
Tips for do's and don'ts
Do's | Don'ts |
---|---|
Conduct thorough feasibility studies | Rush the implementation without proper planning |
Invest in employee training programs | Ignore the importance of workforce adaptation |
Start with scalable solutions | Overlook system scalability and integration issues |
Monitor system performance regularly | Neglect regular maintenance and updates |
Engage stakeholders in planning | Exclude key stakeholders from decision-making |
Click here to read our expertly curated top picks!
Conclusion
Summary of Key Points
Automation systems have emerged as a transformative force in manufacturing, offering numerous benefits such as increased productivity, improved quality, and enhanced cost-efficiency. By automating repetitive tasks and optimizing workflows, manufacturers can achieve faster production rates and maintain high standards of quality. The integration of advanced technologies such as AI, IoT, and cloud computing further enhances the capabilities of automation systems, creating intelligent and interconnected manufacturing environments.
However, automation systems also pose challenges, including high initial investment, complexity of integration, and workforce adaptation. Manufacturers must address these challenges through strategic planning, phased implementation, and workforce development to realize the full potential of automation systems.
Encouraging Ongoing Adaptation
As the manufacturing industry continues to evolve, professionals must stay abreast of technological advancements and consider integrating automation systems into their strategies for sustained competitiveness and innovation. The continuous evolution of automation systems requires adaptability and a proactive approach to innovation.
By embracing future trends such as AI-driven automation, collaborative robots, and edge computing, manufacturers can enhance their competitiveness and drive innovation in their operations. Ongoing adaptation is essential for achieving manufacturing excellence and ensuring long-term success in a dynamic industry.
Navigate Manufacturing Project Success with Meegle
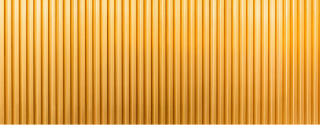
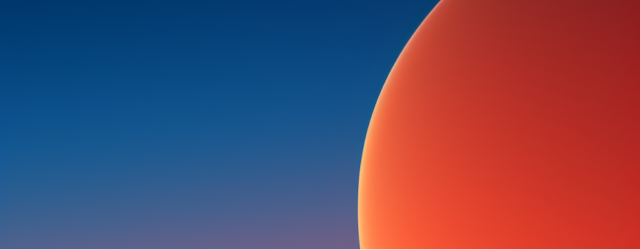
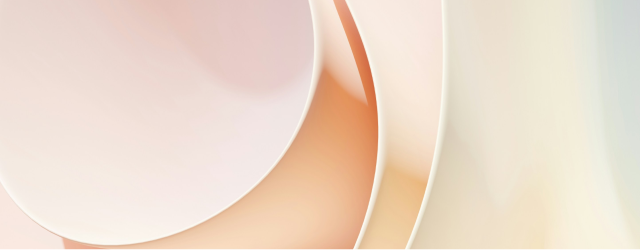
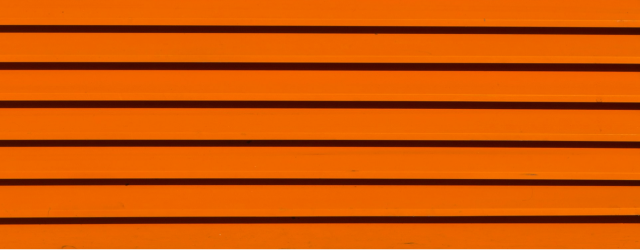
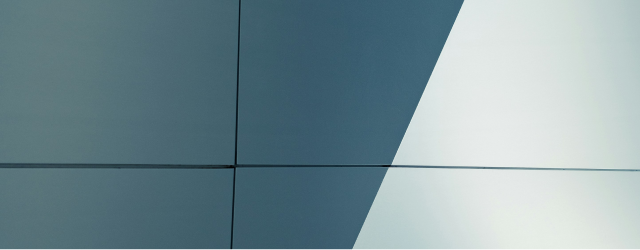
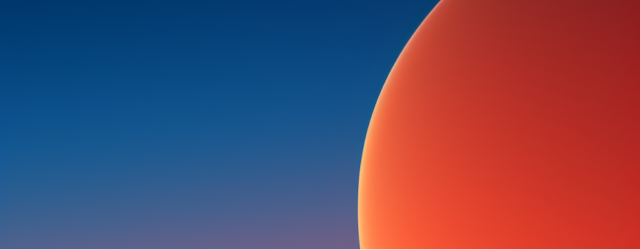
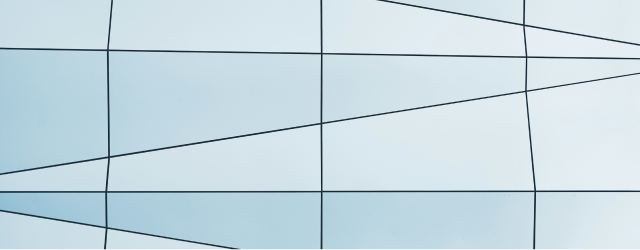
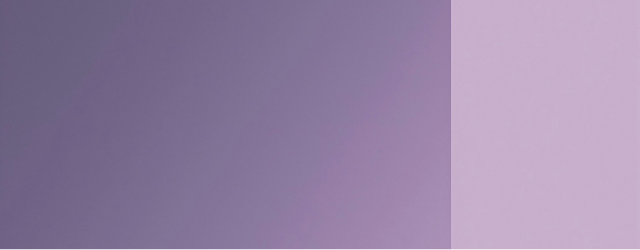