Benchmarking
Gain a thorough understanding of Benchmarking in manufacturing, with insights into their application, benefits, and strategic importance in the industry.
Defining Benchmarking: An Essential Tool
Benchmarking is a methodical process of measuring an organization's performance against industry leaders to identify areas for improvement and innovation. In the manufacturing sector, benchmarking serves as an essential tool for gauging operational efficiency, product quality, and overall competitiveness. By comparing key performance indicators (KPIs) against those of leading competitors or industry standards, manufacturers can pinpoint gaps in their processes and devise strategies to close them. Benchmarking is not merely about imitation but about understanding the best practices that drive success and tailoring these insights to fit one's unique circumstances. It allows manufacturers to set realistic performance targets, track progress, and implement changes that lead to substantial improvements in productivity and profitability.
Enhancing Operational Efficiency Through Benchmarking
The role of benchmarking in boosting operational efficiency cannot be overstated. By systematically comparing processes and performance metrics with those of industry leaders, manufacturers can streamline their operations, improve product quality, and enhance customer satisfaction. For instance, Toyota's implementation of lean manufacturing principles, heavily reliant on benchmarking, has been instrumental in achieving its reputation for high-quality and efficient production. In addition to quality improvements, benchmarking can significantly impact a company's bottom line by reducing waste, optimizing resource utilization, and cutting costs. Furthermore, it fosters a culture of continuous improvement, encouraging employees to regularly evaluate and refine their practices. In a competitive marketplace, where consumers demand superior products at lower prices, benchmarking equips manufacturers with the insights needed to remain agile and responsive to market shifts.
Navigate Manufacturing Project Success with Meegle
Historical development of benchmarking
Tracing the Origins of Benchmarking
The concept of benchmarking has its roots in the early industrial revolution when businesses began recognizing the importance of comparing their practices to those of more successful competitors. Initially, these comparisons were informal, relying on observation and anecdotal evidence. However, as industries grew more complex, the need for a structured approach became apparent. One of the earliest formal applications of benchmarking can be traced back to the 1970s when Xerox Corporation pioneered the practice to regain its competitive edge in the copier market. By meticulously analyzing the production processes of its Japanese competitors, Xerox was able to identify inefficiencies and implement strategic changes that revolutionized its operations. This historical context underscores the enduring relevance of benchmarking as a tool for achieving excellence in manufacturing.
Evolution and Technological Advancements
Over the decades, benchmarking has evolved from a rudimentary practice into a sophisticated, data-driven process facilitated by technological advancements. The advent of digital technologies has transformed the way benchmarking is conducted, enabling manufacturers to collect, analyze, and act upon vast amounts of data with unprecedented speed and accuracy. Innovations such as Enterprise Resource Planning (ERP) systems, data analytics, and cloud computing have enhanced the ability to track and compare performance metrics across various departments and locations. Moreover, the integration of artificial intelligence (AI) and machine learning (ML) has further refined benchmarking methodologies, offering predictive insights and automating routine data analysis tasks. These technological advancements have not only streamlined the benchmarking process but have also expanded its scope, allowing manufacturers to benchmark against a wider range of performance indicators and gain deeper insights into their operations.
Click here to read our expertly curated top picks!
Core principles and techniques of benchmarking
Fundamental Concepts of Benchmarking
The success of any benchmarking initiative hinges on a firm grasp of its core principles. At its heart, benchmarking involves the systematic collection and analysis of performance data to identify best practices and performance gaps. Key performance indicators (KPIs) play a crucial role in this process, serving as the metrics by which performance is assessed. KPIs could include production speed, defect rates, cost per unit, and customer satisfaction levels, among others. Establishing clear, quantifiable KPIs is essential for effective benchmarking, as they provide a baseline against which progress can be measured. Additionally, benchmarking requires a commitment to continuous improvement, with organizations regularly revisiting and refining their benchmarks to adapt to changing conditions and new insights.
Strategic Implementation Techniques
Implementing benchmarking effectively requires a strategic approach that encompasses several key techniques. Firstly, comparative analysis is fundamental, involving the detailed examination of performance data to identify discrepancies between one's operations and those of industry leaders. This analysis can be conducted internally, across different departments, or externally against competitors and industry standards. Another crucial technique is best practice sharing, where organizations identify and adopt the strategies that have proven successful elsewhere. This may involve collaborations or partnerships with other companies, industry forums, or consultancy services. Moreover, setting realistic goals based on benchmarking insights is vital, ensuring that the organization is neither complacent nor overstretching its resources. By adopting a structured approach to benchmarking, manufacturers can systematically enhance their processes and achieve sustained improvements in performance.
Benefits and challenges of benchmarking
Production Advantages and Operational Improvements
The benefits of benchmarking in manufacturing are manifold, encompassing both tangible and intangible gains. One of the most significant advantages is the enhancement of production efficiency. By identifying best practices and performance gaps, manufacturers can streamline their operations, reduce waste, and optimize resource utilization. For example, benchmarking can reveal areas where automation could be implemented to speed up production lines or highlight processes that are causing bottlenecks. Additionally, benchmarking fosters a culture of continuous improvement, encouraging employees to seek out ways to enhance their performance and innovate. This cultural shift can lead to increases in employee satisfaction and retention, as staff feel empowered and valued. In terms of cost reduction, benchmarking helps identify inefficiencies that can be addressed to lower production costs and increase profitability. Furthermore, by improving product quality and customer satisfaction, manufacturers can strengthen their brand reputation and gain a competitive edge in the market.
Navigating Potential Limitations and Challenges
Despite its numerous benefits, implementing benchmarking in manufacturing is not without challenges. One of the primary obstacles is the availability and accuracy of data. Without reliable data, the results of benchmarking efforts may be skewed or misleading, leading to misguided strategies. Additionally, there may be resistance to change within the organization, with employees hesitant to adopt new practices or technologies. This resistance can be mitigated through effective communication and involving employees in the benchmarking process from the outset. Another challenge is the risk of focusing too narrowly on benchmarking, to the detriment of other strategic initiatives. It's crucial for organizations to balance benchmarking with other business priorities and ensure that it aligns with their overall strategic objectives. Lastly, the dynamic nature of the manufacturing industry means that benchmarks must be regularly updated to reflect changing conditions and new insights. Failure to do so can result in benchmarks that are no longer relevant or useful, undermining the effectiveness of the initiative.
Click here to read our expertly curated top picks!
Case studies and real-world applications
Successful industry examples
Successful industry examples
Toyota's Lean Manufacturing
One of the most cited examples of successful benchmarking in the manufacturing industry is Toyota's implementation of lean manufacturing principles. Toyota benchmarked its production processes against those of its competitors and identified inefficiencies that could be addressed through lean methodologies. By focusing on waste reduction, continuous improvement, and employee empowerment, Toyota revolutionized its operations, achieving significant gains in productivity and product quality. This approach has been widely adopted across industries, demonstrating the transformative power of effective benchmarking.
General Electric's Six Sigma
General Electric (GE) is another prime example of a company that has leveraged benchmarking to drive operational excellence. Through its Six Sigma initiative, GE benchmarked its processes against industry standards to identify areas for improvement. By implementing rigorous quality control measures and focusing on defect reduction, GE was able to enhance product quality, reduce costs, and increase customer satisfaction. This case highlights the importance of benchmarking in achieving world-class performance in manufacturing.
Analyzing impact and quantifiable improvements
Analyzing impact and quantifiable improvements
The impact of benchmarking can be clearly seen in the quantifiable improvements achieved by companies that have successfully implemented the practice. For instance, Honeywell International reported a 4% increase in productivity and a 10% reduction in production costs after adopting benchmarking and continuous improvement initiatives. Similarly, Ford Motor Company achieved a 15% reduction in manufacturing cycle times and a significant improvement in product quality through its benchmarking efforts. These measurable outcomes underscore the critical role of benchmarking in driving operational improvements and enhancing competitiveness. Furthermore, these successes have broader implications for industry standards and practices, as companies that excel through benchmarking often set new benchmarks for others to follow.
Technological integration and innovations in benchmarking
Leveraging Current Technologies for Benchmarking
The integration of modern technologies has revolutionized benchmarking practices in manufacturing, offering new avenues for data collection, analysis, and application. Data analytics tools, for example, allow manufacturers to process large volumes of data quickly and accurately, providing insights that were previously unattainable. These tools can help identify patterns and trends, offering a deeper understanding of performance metrics and enabling more informed decision-making. Additionally, artificial intelligence (AI) and machine learning (ML) have become integral to modern benchmarking, offering predictive capabilities that can forecast future performance and highlight potential areas for improvement. These technologies also automate routine data analysis tasks, freeing up human resources for more strategic activities. The Internet of Things (IoT) is another critical technology in benchmarking, with connected devices providing real-time data on equipment performance and product quality. By leveraging these technologies, manufacturers can enhance the accuracy and scope of their benchmarking initiatives, driving more effective and sustainable improvements.
Future Trends and Innovations in Benchmarking Technology
As technology continues to evolve, new trends and innovations are set to shape the future of benchmarking in manufacturing. One such trend is the increasing use of digital twins, which create virtual replicas of physical assets, processes, or systems to simulate performance and identify potential improvements. Digital twins can provide manufacturers with a comprehensive view of their operations, enabling more precise benchmarking and optimization efforts. Another emerging trend is the use of blockchain technology to enhance data security and transparency in benchmarking processes. Blockchain can ensure the integrity of benchmarking data, providing a tamper-proof record of performance metrics and benchmarks. Additionally, the rise of collaborative benchmarking platforms is facilitating knowledge sharing and best practice exchange among manufacturers, fostering a more cooperative approach to benchmarking. These innovations promise to further enhance the effectiveness of benchmarking, offering new opportunities for manufacturers to optimize their operations and remain competitive in a rapidly changing industry.
Click here to read our expertly curated top picks!
Tips for effective benchmarking: do's and don'ts
Do's | Don'ts |
---|---|
Clearly define objectives and goals | Overlook the importance of data accuracy |
Involve cross-functional teams | Ignore feedback from relevant stakeholders |
Regularly update benchmarking criteria | Rely solely on past benchmarks without adjustment |
Click here to read our expertly curated top picks!
Conclusion
Recap of Key Insights and Benefits
Throughout this exploration of benchmarking in manufacturing, we have highlighted its critical role in driving operational efficiency, enhancing product quality, and maintaining competitiveness. By providing a structured framework for assessing performance and identifying best practices, benchmarking empowers manufacturers to optimize their processes and achieve strategic objectives. The integration of modern technologies has further enhanced benchmarking practices, offering new opportunities for data-driven insights and continuous improvement.
Encouraging Ongoing Adoption and Integration
We encourage manufacturing professionals to continuously explore and adopt benchmarking opportunities within their operations. Staying updated with industry trends and technological advancements is crucial for maintaining a competitive edge. By fostering a culture of continuous improvement and leveraging benchmarking insights, manufacturers can navigate the challenges of a rapidly evolving industry and achieve sustained success.
Navigate Manufacturing Project Success with Meegle
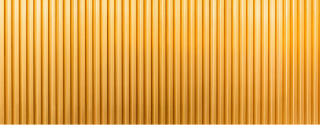
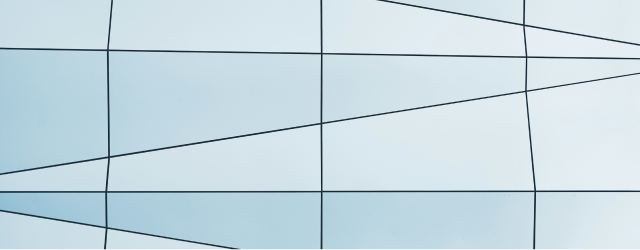
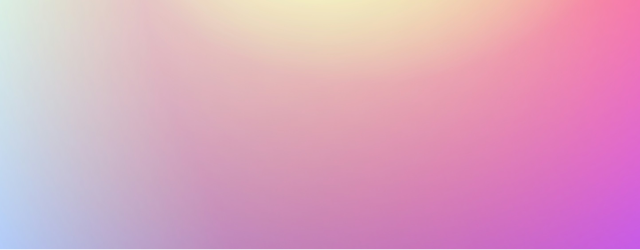
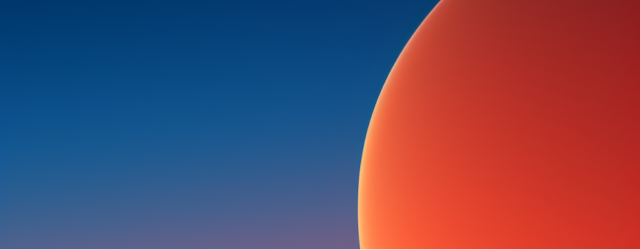
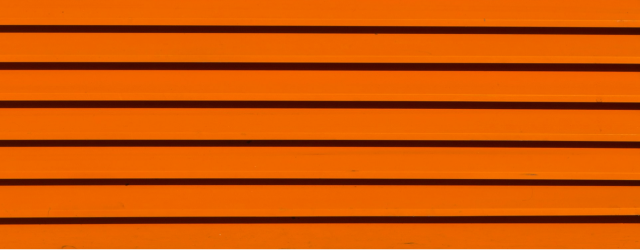
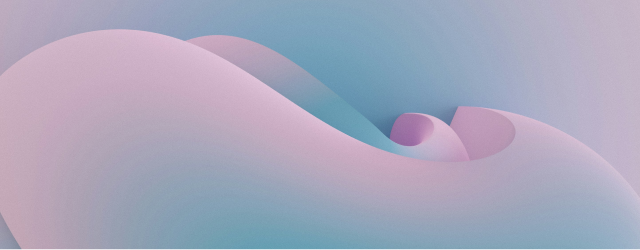
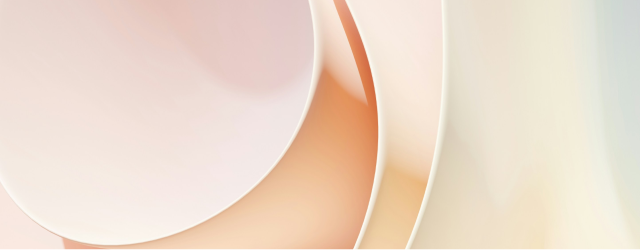
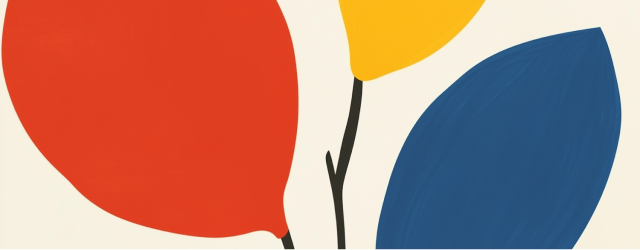