Bill Of Materials (BOM)
Gain a thorough understanding of Bill of Materials (BOM) in manufacturing, with insights into their application, benefits, and strategic importance in the industry.
Defining the Bill of Materials (BOM)
A Bill of Materials (BOM) is a comprehensive list detailing all components, parts, and raw materials required to construct a product. It functions as the foundation of any manufacturing process, providing a structured inventory of items and their quantities needed for production. Typically, a BOM includes information such as part numbers, descriptions, and the hierarchical relationships between various elements. This document is essential in ensuring that manufacturing operations run smoothly and efficiently, as it also outlines the order of assembly and specific instructions for product creation.
There are several types of BOMs, each tailored to different aspects of manufacturing and product management. For instance, an Engineering BOM (EBOM) is primarily used during product design and development phases and includes technical specifications and engineering drawings. In contrast, a Manufacturing BOM (MBOM) focuses on the practical aspects of production, detailing the exact components and processes needed for assembly. Understanding these distinctions is crucial for professionals looking to implement and utilize BOMs effectively across different manufacturing stages.
Importance of BOM in Manufacturing
The importance of a Bill of Materials in manufacturing cannot be overstated. A well-structured BOM enhances production efficiency by offering a clear roadmap for product assembly, thereby minimizing errors and reducing production time. It plays a crucial role in cost management by precisely identifying the materials and quantities required, which aids in accurate budgeting and financial forecasting. By maintaining a detailed BOM, manufacturers can better manage their resources, ensuring optimal allocation and minimizing waste.
Moreover, BOMs contribute significantly to inventory control, providing a centralized reference point for tracking components and adjusting stock levels as needed. This capability is particularly beneficial in just-in-time (JIT) manufacturing environments, where inventory accuracy is vital for maintaining production flow without overstocking. BOMs also facilitate better collaboration and communication across departments, as they provide a unified understanding of product requirements and assembly processes. This shared knowledge base can lead to improved coordination between design, engineering, procurement, and production teams, ultimately enhancing overall manufacturing effectiveness.
Navigate Manufacturing Project Success with Meegle
Historical development of bill of materials (bom)
Tracing the Origins of BOM
The concept of a Bill of Materials dates back centuries, originating from the simple lists craftsmen would use to outline materials and components necessary for producing goods. These early BOMs were rudimentary, often handwritten and used solely for internal reference. However, as industrialization took hold in the 19th century, the complexity of products increased, necessitating more detailed and formalized BOMs. This period marked the beginning of structured BOM documentation, laying the groundwork for the more sophisticated systems we see today.
Throughout the 20th century, the evolution of manufacturing processes drove significant advancements in BOM practices. The introduction of assembly lines in the automotive industry, for instance, highlighted the need for precise and organized component lists to ensure efficient production flow. During World War II, the manufacturing boom further accelerated BOM development, as industries required standardized approaches to manage large-scale production operations. These historical milestones were pivotal in shaping the foundational principles of modern BOM systems, emphasizing accuracy, standardization, and scalability.
Evolution and Modernization
The evolution of BOM practices has been profoundly impacted by technological advancements. The transition from manual to digital BOMs in the late 20th century marked a significant shift, as computer-aided design (CAD) and manufacturing (CAM) technologies revolutionized how BOMs were created and managed. This shift enabled greater precision, easier updates, and the ability to handle complex product structures with multiple components and subassemblies. The integration of BOMs with Enterprise Resource Planning (ERP) and Product Lifecycle Management (PLM) systems further streamlined processes, allowing for seamless communication and data sharing across various organizational functions.
In recent decades, the digitization of BOMs has continued to advance, with cloud-based solutions offering enhanced accessibility and collaboration capabilities. These modern systems allow multiple users to access and update BOM data in real-time, ensuring that all stakeholders have the most current information at their fingertips. Additionally, automation technologies have introduced new efficiencies in BOM management, reducing manual data entry and minimizing errors. As we move forward, the continued evolution and modernization of BOM practices will be driven by emerging technologies such as the Internet of Things (IoT) and artificial intelligence (AI), which promise to further enhance the accuracy, efficiency, and adaptability of BOM systems.
Click here to read our expertly curated top picks!
Core principles and techniques of bom
Essential Concepts of BOM
At the heart of a Bill of Materials lies a few fundamental concepts that are crucial for its effective utilization in manufacturing. A BOM consists of several key components, including part numbers, descriptions, quantities, and units of measure. Each part number is unique, serving as an identifier for the specific component, while descriptions provide detailed information about the item’s characteristics and function. Quantities indicate how many units of each component are required, and units of measure standardize the measurement system used, ensuring clarity and consistency.
Understanding the hierarchy within a BOM is also vital. A BOM can be structured in various ways, often reflecting the complexity and assembly sequence of the product. The top-level item represents the final product or assembly, with subassemblies and individual components listed below. This hierarchical arrangement facilitates an organized view of the product structure, aiding in efficient assembly and resource allocation. The design of a BOM should be meticulous, with careful attention to detail, as even minor inaccuracies can lead to production delays and increased costs.
Implementation Techniques
Implementing an effective BOM system in a manufacturing environment requires a strategic approach and the right tools. One of the first steps is to establish clear guidelines and standards for BOM creation, ensuring consistency across all product lines. This involves defining a standardized format that includes all necessary information, such as part numbers, descriptions, and quantities. Regular training sessions for staff are essential to familiarize them with these standards and best practices, promoting accuracy and efficiency in BOM management.
Digital tools and software solutions play a crucial role in BOM implementation. Modern manufacturing environments benefit from dedicated BOM management software that integrates with existing ERP and PLM systems, streamlining data flow and ensuring all departments have access to up-to-date information. These tools also offer features such as automated updates, version control, and change tracking, minimizing errors and improving overall BOM accuracy. Additionally, leveraging cloud-based solutions allows for greater collaboration and flexibility, as team members can access and modify BOM data from anywhere, at any time.
Benefits and challenges of bom
Enhancing Production with BOM
The advantages of a well-implemented Bill of Materials system are manifold, significantly enhancing production processes and overall manufacturing efficiency. A comprehensive BOM provides a clear and organized framework for product assembly, minimizing errors and reducing production time. By detailing the exact components and quantities needed, BOMs facilitate precise planning and scheduling, ensuring that all necessary materials are available when required. This capability is especially important in just-in-time (JIT) manufacturing environments, where inventory accuracy is crucial for maintaining a steady production flow.
In addition to improving efficiency, BOMs contribute to enhanced quality control and reduced waste. By providing detailed assembly instructions and specifications, BOMs help ensure that products are built to the required standards, minimizing defects and rework. This level of detail also enables manufacturers to identify potential areas for process optimization, leading to further improvements in quality and cost reduction. Furthermore, BOMs promote better collaboration and communication across departments, as they provide a unified understanding of product requirements and assembly processes. This shared knowledge base can lead to improved coordination between design, engineering, procurement, and production teams, ultimately enhancing overall manufacturing effectiveness.
Addressing BOM Challenges
Despite their many benefits, managing a Bill of Materials system is not without challenges. One of the most common issues manufacturers face is maintaining data accuracy. As products evolve and undergo changes, keeping BOMs up-to-date can be a complex task, requiring continuous monitoring and updates. Inaccurate or outdated BOMs can lead to production errors, increased costs, and delays, underscoring the importance of regular audits and data validation processes.
Version control is another significant challenge in BOM management, particularly in environments with frequent product updates or modifications. Without a robust version control system, it can be difficult to track changes and ensure that all stakeholders are working with the most current BOM version. Integration issues can also arise, especially when BOM systems are not properly aligned with other enterprise systems, such as ERP or PLM software. These challenges can be addressed through the implementation of comprehensive training programs, emphasizing the importance of accurate data entry and change management processes. Regular audits and reviews of BOM data are also critical in identifying and rectifying discrepancies, ensuring that the system remains reliable and effective.
Click here to read our expertly curated top picks!
Case studies and real-world applications of bom
Industry success stories
Industry success stories
Examining real-world applications of BOM systems provides valuable insights into their impact on manufacturing operations. One notable example is the aerospace industry, where companies like Boeing have successfully implemented BOM systems to enhance production efficiency and quality control. By leveraging advanced BOM management software, Boeing has been able to streamline its supply chain operations, ensuring that all necessary components are available when needed and reducing production lead times. The company’s commitment to maintaining accurate and up-to-date BOMs has also contributed to improved quality standards, allowing for more efficient assembly processes and reduced rework.
In the automotive sector, Toyota is another case study of effective BOM implementation. Toyota’s renowned production system relies heavily on precise BOM management to support its just-in-time manufacturing approach. By maintaining detailed and accurate BOMs, Toyota ensures that all required parts and components are available at the right time and in the right quantities, minimizing inventory levels and reducing waste. This meticulous attention to BOM accuracy has enabled Toyota to achieve significant cost savings and maintain its competitive edge in the industry.
Measuring bom impact
Measuring bom impact
The impact of BOM systems on manufacturing operations can be quantified through various key performance indicators (KPIs). Metrics such as production lead time, inventory turnover, and defect rates provide valuable insights into the effectiveness of BOM management practices. For instance, companies that have successfully implemented BOM systems often report reduced production lead times, as accurate BOMs facilitate efficient planning and scheduling. Improved inventory turnover rates are another common benefit, as BOMs help ensure that materials are procured and used efficiently, minimizing excess stock and associated carrying costs.
Defect rates and quality performance are also critical indicators of BOM effectiveness. By providing detailed assembly instructions and specifications, BOMs contribute to improved quality control, reducing the likelihood of defects and rework. Companies that have invested in comprehensive BOM systems often report higher quality standards and increased customer satisfaction as a result. These measurable benefits underscore the importance of maintaining accurate and up-to-date BOMs, as they directly impact operational efficiency, cost management, and overall manufacturing success.
Technological integration and innovations in bom
Current BOM Technologies
The technological landscape supporting Bill of Materials systems has evolved significantly, offering a range of tools and solutions to enhance BOM functionality and management. Cloud computing has become a game-changer in BOM management, providing real-time access to BOM data from anywhere, at any time. This accessibility is particularly beneficial for global manufacturing operations, where team members across different locations need to collaborate and share information seamlessly. Cloud-based BOM systems also offer scalability, allowing companies to easily expand their BOM capabilities as their product lines and operations grow.
The Internet of Things (IoT) is another technology that is transforming BOM management by enabling real-time monitoring and data collection from manufacturing processes. IoT devices can provide valuable insights into component usage, performance, and maintenance requirements, allowing for more accurate and dynamic BOM updates. Additionally, artificial intelligence (AI) is being leveraged to automate various aspects of BOM management, such as data entry, error detection, and optimization. AI-powered algorithms can analyze BOM data to identify patterns and trends, offering recommendations for process improvements and cost savings.
Future Trends in BOM
Looking ahead, several emerging trends and innovations are poised to shape the future of Bill of Materials management. One such trend is the increasing use of enhanced automation and robotics in manufacturing processes, which will require more sophisticated BOM systems to manage the complexity and precision of automated operations. Real-time analytics and big data are also set to play a crucial role in BOM management, providing deeper insights into production performance and enabling more informed decision-making.
As digital twin technology continues to gain traction, BOM systems will need to adapt to support virtual representations of physical products and processes. This integration will allow manufacturers to simulate and optimize production scenarios, improving efficiency and reducing risk. Additionally, the growing emphasis on sustainability and environmental responsibility in manufacturing will drive the development of BOM systems that incorporate lifecycle assessment and resource optimization, helping companies reduce waste and minimize their environmental impact. As these trends unfold, manufacturing professionals must stay abreast of technological advancements and continuously adapt their BOM practices to remain competitive in the evolving industry landscape.
Click here to read our expertly curated top picks!
Tips for effective bom management
Do's | Don'ts |
---|---|
Maintain regular audits and updates | Neglect data accuracy and completeness |
Utilize digital tools for BOM management | Rely solely on manual BOM processes |
Train staff on BOM best practices | Overlook the importance of version control |
Integrate BOM with other business systems | Ignore the need for cross-departmental collaboration |
Monitor KPIs to assess BOM effectiveness | Fail to adapt BOM processes to changing needs |
Click here to read our expertly curated top picks!
Conclusion
Recap of Key Insights
In summary, mastering the Bill of Materials (BOM) is essential for modern manufacturing excellence. A well-structured BOM enhances production efficiency, improves quality control, and reduces waste. By providing a comprehensive blueprint for product assembly, BOMs facilitate precise planning and collaboration across departments, ultimately contributing to overall operational success.
Encouragement for Continuous Improvement
As the manufacturing landscape continues to evolve, it is crucial for professionals to continuously adapt their BOM practices to stay competitive. Embracing technological advancements and innovative approaches will ensure that manufacturing operations remain efficient, cost-effective, and responsive to changing market demands. With a commitment to continuous improvement, organizations can harness the full potential of BOM systems to drive future success.
Navigate Manufacturing Project Success with Meegle
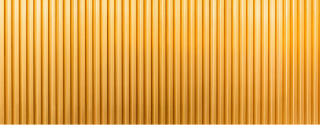
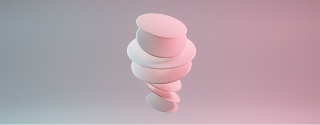
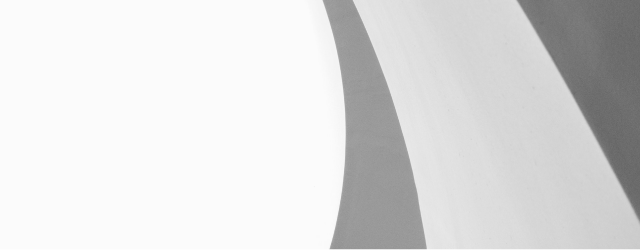
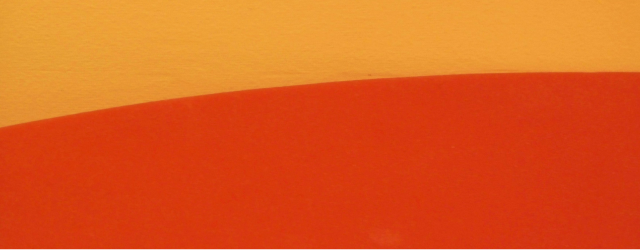
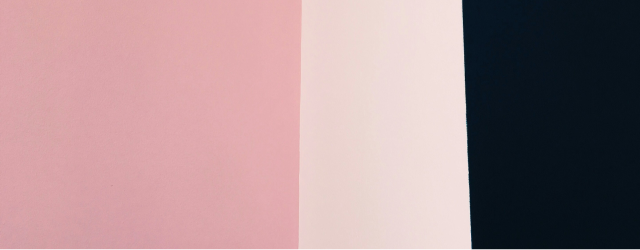
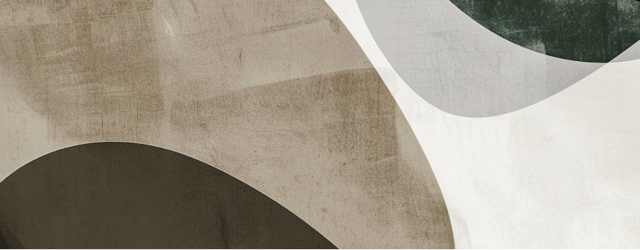
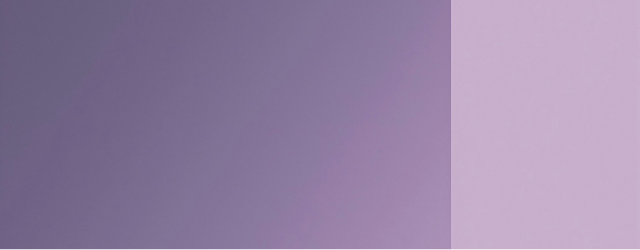
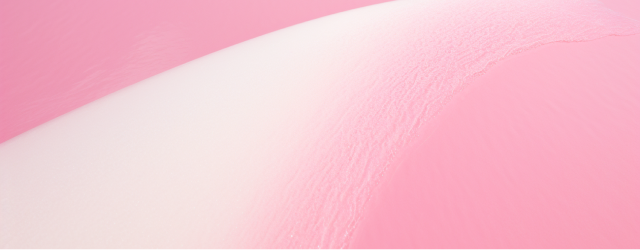