Blow Molding
Gain a thorough understanding of Blow Molding in manufacturing, with insights into their application, benefits, and strategic importance in the industry.
Overview of Blow Molding
Blow molding is a sophisticated manufacturing process designed to produce hollow plastic products. The technique involves heating plastic material until it becomes pliable and then inflating it with air pressure into a mold cavity to create the desired shape. This method is particularly vital across various industries, including automotive, packaging, and consumer goods, where precision and efficiency are paramount. For instance, the automotive industry relies heavily on blow molding to produce lightweight fuel tanks and other components that enhance vehicle performance. In packaging, blow molding is indispensable for creating durable containers and bottles that ensure product safety and longevity.
Moreover, blow molding aligns seamlessly with sustainability goals by reducing waste and incorporating recyclable materials. By utilizing efficient material usage and minimizing production byproducts, blow molding contributes significantly to eco-friendly manufacturing practices. Companies are increasingly adopting this technique to not only improve their production processes but also to meet regulatory requirements for environmental sustainability. Furthermore, advancements in blow molding technology have enabled the use of biodegradable materials, further enhancing its environmental appeal.
Understanding the versatility and application of blow molding is crucial for manufacturers aiming to leverage this technique for operational excellence. It offers a unique balance between cost-effectiveness and high-quality output, making it a preferred choice for large-scale production. In essence, blow molding is not just a manufacturing process; it is a catalyst for innovation and efficiency in the modern industrial landscape.
Role in Manufacturing Efficiency
Blow molding plays a pivotal role in enhancing manufacturing efficiency, significantly speeding up production cycles and enabling high-volume outputs. One of the core advantages of blow molding is its ability to produce consistent product quality by ensuring uniform thickness and structural integrity. This is particularly important in industries where precision and reliability are non-negotiable, such as automotive and pharmaceuticals.
The technique is cost-effective compared to traditional manufacturing methods, primarily due to its ability to produce complex geometries with minimal material waste. Unlike other methods that require extensive machining or assembly, blow molding streamlines the production process, reducing labor costs and time. A prime example is the packaging industry, where blow molding facilitates the rapid creation of bottles and containers that are both lightweight and durable.
Additionally, blow molding is adaptable to producing intricate designs, which is crucial for manufacturers looking to differentiate their products in competitive markets. The ability to mold complex shapes with precision allows companies to innovate and improve their product offerings continuously. Moreover, blow molding supports the production of parts that meet stringent regulatory requirements for safety and quality, ensuring compliance with industry standards.
In summary, the operational efficiency offered by blow molding is unmatched, making it a cornerstone technique in modern manufacturing. Its adaptability, coupled with cost-effectiveness and product quality, positions blow molding as a valuable asset for manufacturers seeking to enhance their production capabilities and maintain a competitive edge.
Navigate Manufacturing Project Success with Meegle
Historical development of blow molding
Origins of Blow Molding
The origins of blow molding can be traced back to the glass industry in the 19th century, where it was initially employed to create hollow glass items. The transition to plastics occurred in the mid-20th century, marking a significant technological evolution. Pioneers in the field, recognizing the potential of plastics, adapted the blow molding technique to accommodate this versatile material. This shift was driven by the demand for cost-effective, mass-produced plastic products, which could not be fulfilled by traditional glass-blowing methods.
One of the key breakthroughs in the adoption of blow molding for plastics was the development of extrusion blow molding. This innovation allowed manufacturers to produce hollow plastic items efficiently, paving the way for widespread use in industries such as packaging and automotive. Early challenges included finding suitable materials that could withstand the heat and pressure involved in the process. Overcoming these hurdles required extensive research and development, leading to the discovery of various polymers suitable for blow molding.
As the technique gained traction, manufacturers began exploring its potential to produce more complex products, expanding its application beyond simple containers and bottles. The evolution of blow molding technology has been marked by continuous improvements in machinery and materials, enabling higher precision and versatility in production. Today, blow molding is a cornerstone of modern manufacturing, thanks to its ability to produce high-quality, cost-effective products at scale.
Evolution Over Time
The evolution of blow molding technology has been characterized by significant advancements, transforming it into a sophisticated manufacturing technique. The introduction of extrusion blow molding and injection blow molding marked major milestones in its development. Extrusion blow molding, for example, became the preferred method for creating large hollow parts, such as automotive fuel tanks and industrial containers, due to its efficiency and adaptability. On the other hand, injection blow molding is ideal for smaller, precision parts, offering high-quality output with minimal material waste.
Innovations such as multi-layered blow molding have further expanded its capabilities, allowing manufacturers to produce complex products with enhanced properties. Multi-layered blow molding involves layering different materials to create products with superior strength, barrier properties, or aesthetic appeal. This technique is particularly beneficial in the packaging industry, where containers must protect contents from external factors while maintaining visual attractiveness.
Moreover, advancements in material science have introduced new polymers and composites with enhanced mechanical and thermal properties, broadening the application scope of blow molding. The integration of automation and Industry 4.0 technologies has also revolutionized blow molding operations, increasing precision, reducing human error, and optimizing production efficiency. Automated systems ensure consistent quality, monitor process variables in real time, and facilitate rapid prototyping, enabling manufacturers to innovate swiftly and effectively.
Overall, the evolution of blow molding reflects the industry's response to changing market demands and technological possibilities. As manufacturers continue to embrace new materials and automated processes, blow molding remains at the forefront of innovation, driving advancements in product design and manufacturing efficiency.
Click here to read our expertly curated top picks!
Core principles and techniques
Fundamental Concepts
Blow molding is grounded in several core principles that are essential for successful execution. Material selection is paramount, as the properties of the chosen polymer dictate the final product’s durability, flexibility, and appearance. Common materials used include polyethylene, polypropylene, and PVC, each offering distinct advantages for specific applications. For instance, polyethylene is favored for its strength and moisture resistance, making it ideal for containers and bottles.
The heating method employed in blow molding plays a crucial role in the process. The plastic must be heated to a precise temperature where it becomes pliable but not molten, allowing it to be inflated into the mold cavity. Controlling temperature is vital to ensure uniform expansion and avoid defects such as thinning or warping. Advanced heating systems are often used to maintain consistent heat distribution, enhancing product quality.
Mold design is another critical component of blow molding, as it determines the shape and texture of the final product. Designing molds requires a thorough understanding of airflow dynamics and material properties, as these factors influence how the plastic expands and cools into the desired form. Precision in mold design ensures that the product meets specified dimensions and structural requirements, eliminating the need for further finishing processes.
Overall, the success of blow molding hinges on meticulous attention to material selection, heating methods, and mold design. By mastering these fundamental concepts, manufacturers can optimize their blow molding operations to produce high-quality, cost-effective products that meet market demands.
Implementation Techniques
Various techniques are employed in blow molding, each offering unique advantages and applications. Extrusion blow molding is widely used for creating large, hollow parts such as automotive fuel tanks and industrial containers. This technique involves extruding melted plastic into a parison or tube, which is then inflated within a mold cavity. Extrusion blow molding is favored for its efficiency and ability to produce complex shapes with uniform thickness.
Injection blow molding, on the other hand, is ideal for smaller, precision parts such as bottles and pharmaceutical containers. In this process, the plastic is first injected into a preform mold and then expanded within a blow mold. Injection blow molding offers superior control over product dimensions and surface finish, making it suitable for applications requiring high quality and consistency.
Stretch blow molding is another technique employed for producing lightweight and durable products. This method involves stretching the plastic both vertically and horizontally before inflating it, enhancing its strength and clarity. Stretch blow molding is commonly used in the beverage industry for manufacturing PET bottles, which must withstand internal pressure and maintain visual appeal.
Choosing the appropriate blow molding technique depends on several factors, including product design, material type, and production volume. Manufacturers must evaluate these criteria to select the most suitable method for their specific application. By understanding the advantages and limitations of each technique, they can optimize their blow molding operations to achieve desired outcomes and enhance production efficiency.
Benefits and challenges
Advantages in Production
Blow molding offers several advantages that make it a preferred choice for mass production. One of the key benefits is its ability to produce lightweight, durable, and customizable products. By using air pressure to mold plastic into intricate shapes, manufacturers can create complex designs that would be challenging to achieve with traditional methods. This versatility allows companies to innovate and differentiate their products in competitive markets, enhancing their strategic positioning.
Efficiency in mass production is another significant advantage of blow molding. The technique streamlines the manufacturing process, reducing labor costs and minimizing material waste. Unlike other methods that require extensive machining or assembly, blow molding facilitates the rapid creation of products, enabling manufacturers to meet high-demand cycles without compromising quality. A prime example is the packaging industry, where blow molding is used to produce large quantities of bottles and containers quickly and cost-effectively.
Moreover, blow molding supports regulatory compliance by producing parts that meet stringent safety and quality standards. The technique ensures uniform thickness and structural integrity, essential for applications where reliability is paramount, such as automotive and pharmaceuticals. By adhering to industry requirements, manufacturers can maintain customer trust and enhance market competitiveness.
Overall, the advantages of blow molding in production are manifold, offering a unique blend of efficiency, versatility, and quality. These benefits underscore its importance as a cornerstone technique in modern manufacturing, driving innovation and operational excellence.
Potential Limitations
Despite its advantages, blow molding presents certain challenges that manufacturers must address to optimize their operations. One limitation is the compatibility of materials used in the process. Not all polymers are suitable for blow molding, as some may not withstand the heat and pressure involved. Manufacturers must select materials carefully, based on their properties and intended application, to avoid defects such as thinning or warping.
The complexity of mold design is another challenge, as it requires precision and expertise to ensure the final product meets specified dimensions and aesthetics. Designing molds necessitates a thorough understanding of airflow dynamics and material properties, as these factors influence how the plastic expands and cools into shape. Any miscalculations can result in product inconsistencies, affecting quality and performance.
Issues with product uniformity can also arise, demanding precise control over process variables such as temperature and pressure. Variations in these parameters can lead to defects or compromised structural integrity, necessitating rigorous monitoring and adjustment during production. Manufacturers must invest in advanced control systems to maintain consistency and optimize product quality.
To mitigate these challenges, ongoing research and development are crucial. Innovations in material science and automation can enhance blow molding capabilities, addressing limitations and improving efficiency. By embracing new technologies and refining processes, manufacturers can overcome obstacles and leverage blow molding for superior outcomes in their operations.
Click here to read our expertly curated top picks!
Case studies and real-world applications
Industry examples
Industry examples
Blow molding has been successfully integrated into various industries, demonstrating its versatility and effectiveness in enhancing product offerings. In the automotive sector, companies like Ford and General Motors have utilized blow molding to produce lightweight fuel tanks and other components, improving vehicle performance and fuel efficiency. The ability to create complex shapes with precision has enabled these manufacturers to innovate continually, meeting evolving market demands and regulatory requirements.
In the pharmaceutical industry, blow molding is employed to create containers and bottles that ensure product safety and integrity. Companies such as Pfizer leverage this technique to produce high-quality packaging that meets stringent standards for health and safety. Blow molding's capability to produce uniform and durable products is crucial in this sector, where reliability is paramount.
The food packaging industry also benefits significantly from blow molding, with giants like Coca-Cola and Nestlé adopting the technique to produce bottles and containers that preserve freshness and extend shelf life. Blow molding offers a cost-effective solution for mass-producing packaging that meets consumer expectations for convenience and sustainability. By leveraging blow molding, these companies have enhanced their strategic positioning and maintained competitiveness in a dynamic market.
Overall, the integration of blow molding across diverse industries showcases its strategic advantages in product innovation, quality assurance, and operational efficiency. These examples underscore the technique's role as a catalyst for growth and success in modern manufacturing.
Impact analysis
Impact analysis
The tangible impacts of blow molding on production efficiency, cost reduction, and product quality are profound. By streamlining manufacturing processes, blow molding enables companies to produce high volumes of products quickly and cost-effectively. This efficiency translates into reduced labor costs and minimized material waste, enhancing profitability and market competitiveness.
Product quality is another area where blow molding excels, ensuring uniform thickness and structural integrity across all items produced. This consistency is vital for industries where reliability and performance are non-negotiable, such as automotive and pharmaceuticals. By maintaining high-quality standards, manufacturers can build trust with customers and differentiate their offerings in competitive markets.
Moreover, blow molding's ability to produce complex shapes with precision allows companies to innovate continually, meeting evolving consumer demands and industry regulations. The technique supports product customization and differentiation, enabling manufacturers to maintain a strategic edge. Companies that have strategically implemented blow molding have realized long-term benefits, including enhanced customer satisfaction, improved market positioning, and sustained growth.
In summary, blow molding's impact on manufacturing is multifaceted, driving efficiency, innovation, and quality in production processes. As companies continue to optimize their operations with blow molding, they can achieve superior outcomes and maintain competitiveness in a rapidly changing industrial landscape.
Technological integration and innovations
Current Technologies
Current technologies complement blow molding, enhancing its capabilities and optimizing production processes. Computer-aided design (CAD) software plays a crucial role in mold design, allowing manufacturers to create precise and complex molds that meet specific product requirements. Advanced CAD systems facilitate rapid prototyping and design adjustments, enabling companies to innovate swiftly and effectively.
Robotics and automation are increasingly integrated into blow molding operations, reducing human error and increasing precision. Automated systems ensure consistent quality, monitor process variables in real time, and optimize production efficiency. By leveraging robotics, manufacturers can enhance their operational capabilities and maintain a competitive edge in the market.
Advancements in material science have also expanded the application scope of blow molding, with new polymers and composites offering enhanced mechanical and thermal properties. These materials enable the production of high-performance products with superior strength, durability, and aesthetic appeal. Companies are increasingly adopting eco-friendly and sustainable materials, aligning with regulatory requirements and consumer preferences for environmentally responsible products.
Furthermore, innovations in sensor technology and data analytics have revolutionized blow molding operations, facilitating real-time process monitoring and optimization. By harnessing these technologies, manufacturers can maintain consistent quality, reduce waste, and improve overall production efficiency.
Future Trends
Future developments in blow molding are poised to focus on sustainability and smart manufacturing, driven by evolving industry standards and consumer preferences. Emerging technologies such as 3D blow molding hold the potential to revolutionize production processes, enabling the creation of intricate designs with minimal material waste. This technique offers enhanced precision and versatility, supporting product innovation and customization.
The integration of artificial intelligence (AI) for predictive maintenance and quality assurance is another trend that promises to enhance blow molding operations. AI systems can analyze process data to identify potential issues and optimize production variables, ensuring consistent quality and reducing downtime. By leveraging AI technology, manufacturers can improve operational efficiency and maintain competitive advantage in the market.
Sustainability is a key focus area, with companies increasingly adopting biodegradable materials and energy-efficient technologies to align with environmental goals. The use of recyclable and eco-friendly polymers can reduce waste and meet regulatory requirements for sustainable manufacturing. Manufacturers are also exploring innovative approaches to recycling and reusing materials, enhancing their commitment to environmental responsibility.
Overall, the future of blow molding is characterized by innovation and sustainability, with advancements in technology driving improvements in product design, quality, and efficiency. As companies embrace these trends, they can enhance their operations and maintain competitiveness in a rapidly evolving industrial landscape.
Click here to read our expertly curated top picks!
Tips for do's and dont's
Do's | Dont's |
---|---|
Select high-quality materials suited for blow molding | Avoid using incompatible materials |
Ensure precise mold design for optimal product shape | Do not neglect mold maintenance |
Regularly monitor process variables for consistency | Don't overlook safety protocols |
Invest in technology upgrades for efficiency | Avoid cutting costs on essential equipment |
Click here to read our expertly curated top picks!
Conclusion
Summary of Key Points
Throughout this article, we have explored the multifaceted aspects of blow molding, from its historical development to its core principles and techniques. Blow molding has emerged as a transformative manufacturing process, offering unparalleled efficiency and versatility in producing hollow plastic products. Its benefits in production include the ability to create lightweight, durable, and customizable items, while challenges such as material compatibility and mold design complexity require ongoing research and development. Real-world applications across industries like automotive, pharmaceuticals, and food packaging showcase blow molding's strategic advantages in innovation and quality assurance.
Encouraging Ongoing Adaptation
As blow molding continues to evolve, professionals must stay updated on advancements and consider integrating its techniques into their manufacturing strategies. The potential for blow molding to drive innovation, efficiency, and sustainability in production processes is immense. By embracing new technologies and optimizing operations, manufacturers can maintain competitiveness and achieve superior outcomes in their industries. Encouraging ongoing adaptation to blow molding developments is crucial for leveraging its full potential and ensuring sustained growth and success in modern manufacturing.
Navigate Manufacturing Project Success with Meegle
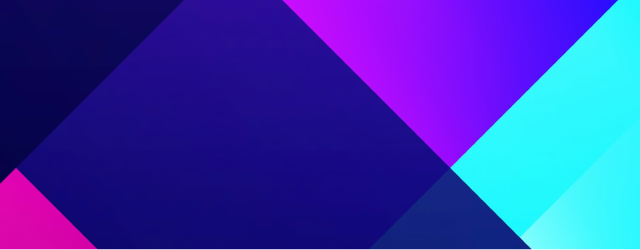
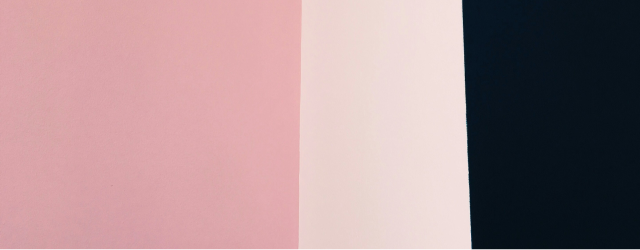
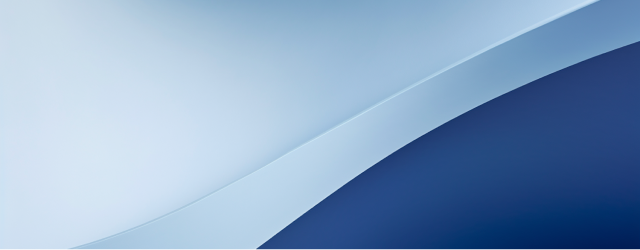
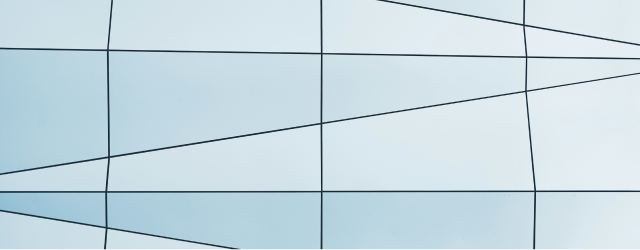
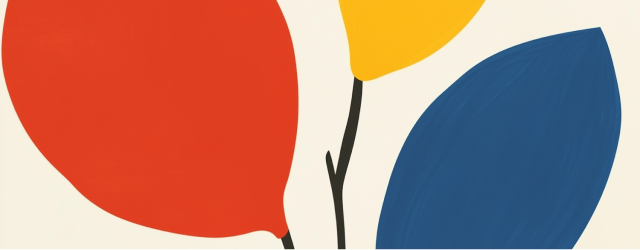
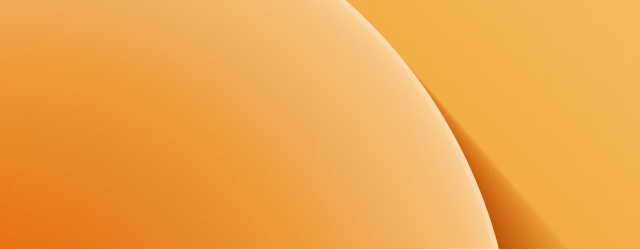
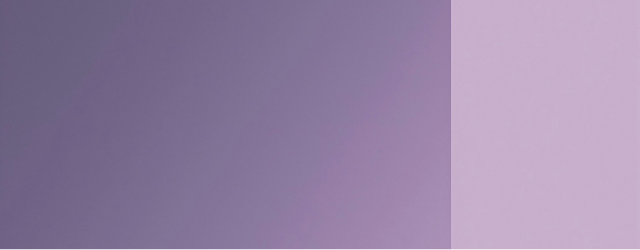
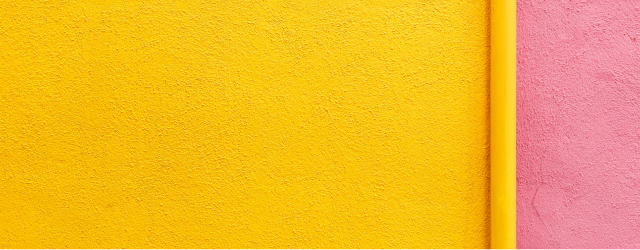