Brazing And Soldering
Gain a thorough understanding of Brazing and Soldering in manufacturing, with insights into their application, benefits, and strategic importance in the industry.
Overview of Brazing and Soldering
Brazing and Soldering are metal joining techniques that play a fundamental role in various manufacturing sectors. Though they are often mentioned together, they differ significantly in their methods and applications. Brazing involves joining materials using a filler metal with a melting point above 450°C, but below that of the base metals. The process relies on capillary action to distribute the molten filler between the closely fitted surfaces, creating a strong, leak-proof joint upon cooling. Soldering, on the other hand, employs filler metals with melting points below 450°C, typically using a soldering iron or gun to melt the solder, which also uses capillary action to form the joint.
These techniques are indispensable in sectors such as electronics, automotive, and aerospace due to their ability to join metals with precision and efficiency. In electronics, for instance, soldering is used to assemble circuit boards, while brazing is crucial in the automotive industry for constructing heat exchangers and fuel lines. The versatility of Brazing and Soldering allows manufacturers to select the most appropriate method based on the materials and desired properties of the joint, thus ensuring optimal performance and reliability of the final product. Their ability to join dissimilar metals and materials further enhances their applicability, making them essential in the production of complex assemblies and structures.
Role in Manufacturing Efficiency
Brazing and Soldering significantly enhance manufacturing efficiency by facilitating faster production cycles, precise joint formation, and increased durability of components. These techniques allow manufacturers to produce high-quality goods with tight tolerances, which are essential in sectors like aerospace and electronics where precision is paramount. The ability to create strong, reliable joints without altering the base metals' properties contributes to the longevity of products, reducing the need for frequent repairs or replacements.
In terms of cost savings, Brazing and Soldering present a more economical option compared to welding or other joining methods, especially when dealing with thin or intricate components. The processes are less energy-intensive, minimizing production costs and enhancing sustainability. Moreover, the reduced thermal impact on the materials helps preserve their structural integrity, preventing warping or degradation. As manufacturers strive for sustainable practices, Brazing and Soldering offer significant advantages, such as lower emissions and energy consumption. These techniques are integral to achieving a competitive edge by streamlining production processes, improving product quality, and supporting eco-friendly initiatives.
Navigate Manufacturing Project Success with Meegle
Historical development of brazing and soldering
Origins of Brazing and Soldering
The history of Brazing and Soldering is deeply intertwined with the evolution of human engineering and construction efforts. Dating back thousands of years, these techniques have roots in ancient practices where artisans and craftsmen utilized simple methods to join metals for tools and decorative items. Early evidence of brazing can be traced back to Egyptian and Mesopotamian civilizations, where artisans used copper and gold brazing techniques to create intricate jewelry and artifacts.
The initial uses of these processes were not just limited to aesthetics; they played a significant role in the development of early engineering projects. For instance, soldering was pivotal in creating the first metal weapons and armor, enhancing their durability and effectiveness in combat. As civilizations advanced, so did the sophistication of brazing and soldering methods, evolving from rudimentary practices to more refined techniques. The significance of these processes in early engineering cannot be overstated, as they laid the groundwork for modern metalworking applications.
Evolution Over Time
Over the centuries, Brazing and Soldering have undergone substantial advancements, driven by innovations in materials, temperatures, and methodologies. The Industrial Revolution marked a significant turning point, with the introduction of new alloys and heating technologies that expanded the capabilities of these techniques. The development of specialized fluxes and filler materials further improved the effectiveness of brazing and soldering, enabling the creation of stronger, more reliable joints.
In modern times, technological innovations such as induction brazing and advanced soldering techniques have revolutionized the industry, allowing for greater precision and control in the joining process. These advancements have been instrumental in adapting brazing and soldering to contemporary manufacturing needs, ensuring their continued relevance and applicability. The role of innovation in shaping these processes cannot be underestimated, as it has paved the way for improved efficiency, sustainability, and quality in metal joining applications.
Click here to read our expertly curated top picks!
Core principles and techniques
Fundamental Concepts
Understanding the fundamental principles of Brazing and Soldering is crucial for effectively applying these techniques in manufacturing. Both processes rely on the use of filler metals to join base materials, with the choice of filler and fluxes playing a critical role in determining the strength and quality of the joint. Fluxes are chemical agents used to prevent oxidation and facilitate the flow of the filler metal, ensuring a clean and strong bond.
Melting points are a key consideration, with brazing involving higher temperatures compared to soldering. The selection of appropriate melting points is essential for achieving the desired joint characteristics without compromising the base materials. Joint design is another vital aspect, as it dictates the distribution and flow of the filler metal, influencing the overall strength and durability of the connection. The scientific basis for these processes is rooted in metallurgical principles, which govern the interactions between metals and the formation of alloys. By understanding these concepts, manufacturers can optimize their brazing and soldering practices, ensuring high-quality outcomes in their production processes.
Implementation Techniques
Implementing Brazing and Soldering techniques requires a strategic approach to achieve optimal results. Various methods are available, each with distinct advantages depending on the materials and applications involved. Torch brazing is a widely used technique, ideal for small to medium-sized components requiring precise heat application. Furnace brazing offers uniform heating and is suitable for batch processes, ensuring consistent quality across multiple parts.
Induction brazing is a more advanced method, utilizing electromagnetic fields to generate heat, offering precise control over the temperature and heating duration. This technique is particularly beneficial for joining sensitive materials that require minimal thermal impact. Soldering techniques, such as wave and reflow soldering, are commonly used in electronics manufacturing, providing efficient solutions for assembling circuit boards and electronic components. The selection of the appropriate method is crucial, as it directly impacts the efficiency and effectiveness of the brazing or soldering process. By understanding the nuances of each technique, manufacturers can tailor their approach to meet specific material and application requirements, ensuring optimal performance and reliability.
Benefits and challenges
Advantages in Production
Brazing and Soldering offer numerous benefits in production, making them indispensable in manufacturing processes. These techniques produce strong joints that can withstand significant stress and environmental factors, ensuring the longevity and reliability of the final product. Their versatility allows for joining a wide range of materials, including dissimilar metals, plastics, and ceramics, expanding their applicability across various industries.
Cost-effectiveness is another major advantage, as these processes typically require less energy and resources compared to other joining methods. The ability to create complex assemblies with minimal material waste enhances sustainability and supports eco-friendly initiatives. Specific scenarios highlight where Brazing and Soldering excel, such as in the automotive industry for constructing lightweight heat exchangers and fuel lines, or in electronics for assembling delicate circuit boards. The combination of strong joints, versatility, and cost-effectiveness makes Brazing and Soldering essential techniques for achieving superior production outcomes.
Potential Limitations
Despite their benefits, Brazing and Soldering also present several challenges that manufacturers must navigate. Material compatibility is a primary concern, as certain metals may react adversely with filler materials or fluxes, compromising the strength and durability of the joint. Joint longevity can be impacted by factors such as environmental exposure or mechanical stress, requiring careful selection of materials and design considerations.
Process complexity is another challenge, particularly for intricate assemblies requiring precise temperature control and filler distribution. Overcoming these limitations requires strategic planning and execution, such as thorough material testing and selection, optimizing joint design, and careful monitoring of process parameters. By addressing these challenges, manufacturers can maximize the potential of Brazing and Soldering, ensuring high-quality outcomes and efficient production processes.
Click here to read our expertly curated top picks!
Case studies and real-world applications
Industry examples
Industry examples
Automotive Industry
In the automotive industry, Brazing and Soldering are pivotal in manufacturing essential components like heat exchangers and fuel lines. These techniques enable the creation of lightweight yet durable joints, crucial for enhancing vehicle efficiency and performance. For example, brazing is used to join aluminum components in heat exchangers, optimizing thermal conductivity and minimizing energy consumption. Soldering plays a critical role in electronics integration, ensuring reliable connections for sensors and control systems.
Aerospace Industry
The aerospace industry relies heavily on brazing and soldering for constructing critical components such as turbine engines and airframes. Brazing is particularly important for joining high-strength alloys used in turbine blades, enabling them to withstand extreme temperatures and pressures. Soldering is essential in assembling electronic systems and connections within the cockpit and control panels, ensuring seamless communication and navigation.
Electronics Industry
In the electronics industry, brazing and soldering are employed extensively in circuit board assemblies and delicate connections. Soldering is crucial for attaching components like resistors and capacitors, providing reliable electrical conductivity and minimizing signal loss. Brazing is used in heat sinks and thermal management systems, ensuring efficient heat dissipation and prolonging the lifespan of electronic devices.
Impact analysis
Impact analysis
The measurable impacts of Brazing and Soldering in these industries are profound, resulting in significant improvements in quality, efficiency, and cost. In the automotive sector, the use of brazing and soldering has led to increased fuel efficiency and reduced emissions, supporting sustainability initiatives. The aerospace industry benefits from the enhanced reliability and performance of components, ensuring safety and longevity in flight operations.
In electronics, brazing and soldering contribute to the production of high-quality devices with minimal defects, reducing the need for repairs and replacements. The cost savings associated with these processes are substantial, as manufacturers can produce complex assemblies efficiently with minimized material waste. By leveraging Brazing and Soldering, industries can achieve superior outcomes, enhancing their competitiveness and supporting sustainable practices.
Technological integration and innovations
Current Technologies
Current technologies are continuously enhancing Brazing and Soldering processes, with robotics and advanced materials playing a significant role. Robotics provide precise control and automation, improving the efficiency and consistency of brazing and soldering applications. Advanced materials, such as high-performance alloys and fluxes, enable stronger and more reliable joints, expanding the capabilities of these techniques.
The integration of AI and machine learning offers further optimization, allowing manufacturers to predict outcomes and adjust process parameters in real-time. These technologies facilitate adaptive control, ensuring optimal performance and quality in metal joining applications. By embracing current technologies, manufacturers can enhance their brazing and soldering processes, achieving superior results and supporting innovation.
Future Trends
Future innovations in Brazing and Soldering are poised to revolutionize the industry, with nanotechnology and environmentally friendly practices leading the way. Nanotechnology offers the potential to create ultra-strong joints with minimal material use, enhancing efficiency and sustainability. Environmentally friendly practices, such as the development of non-toxic fluxes and filler materials, support eco-friendly manufacturing initiatives.
Potential shifts in industry standards and practices are likely, influenced by emerging technologies and the demand for sustainable solutions. Manufacturers must stay informed and adaptable, integrating new techniques and technologies into their strategies to remain competitive. By anticipating future trends, industries can leverage Brazing and Soldering for continued growth and innovation.
Click here to read our expertly curated top picks!
Tips for do's and don'ts
Do's | Don'ts |
---|---|
Ensure proper cleaning of the surfaces to be joined | Avoid overheating the materials |
Choose the right filler material for the application | Do not neglect safety precautions |
Maintain the correct temperature control during the process | Avoid using incompatible fluxes |
Follow manufacturer guidelines for equipment use | Do not rush the cooling process |
Click here to read our expertly curated top picks!
Conclusion
Summary of Key Points
Brazing and Soldering are integral to modern manufacturing, offering precise and efficient solutions for joining metals and other materials. These techniques provide numerous benefits, including strong joints, versatility, and cost-effectiveness, making them essential in industries like automotive, aerospace, and electronics. Despite challenges such as material compatibility and process complexity, strategic planning and execution can optimize outcomes. Technological advancements continue to enhance these processes, supporting innovation and sustainability.
Encouraging Ongoing Adaptation
Professionals are encouraged to stay informed and consider integrating Brazing and Soldering into their manufacturing strategies. The importance of adaptability cannot be overstated, as leveraging these techniques can significantly improve production outcomes. By embracing technological advancements and anticipating future trends, manufacturers can ensure continued growth and success in the competitive landscape.
Navigate Manufacturing Project Success with Meegle
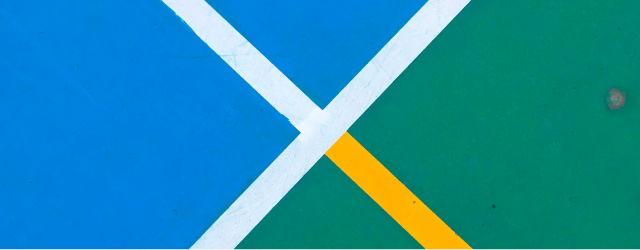
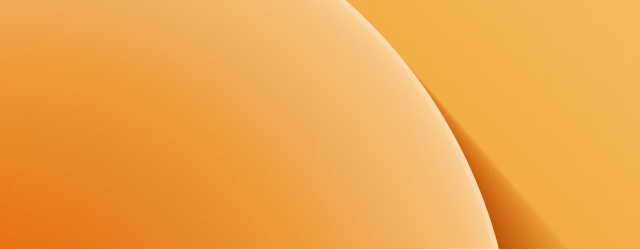
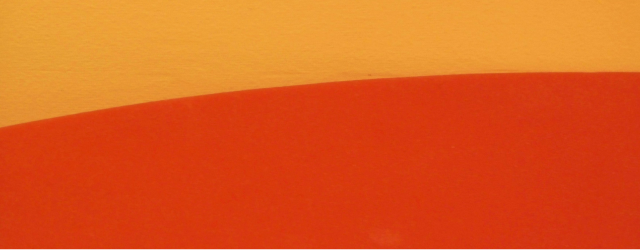
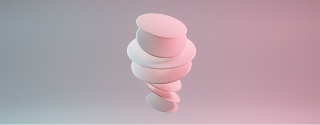
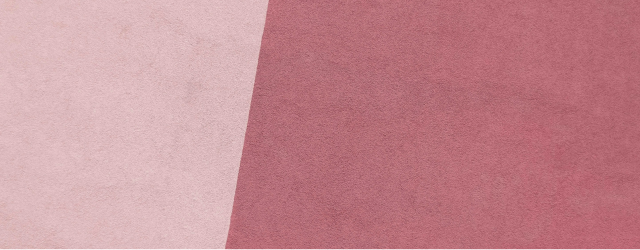
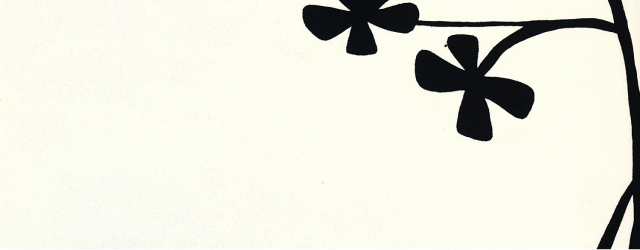
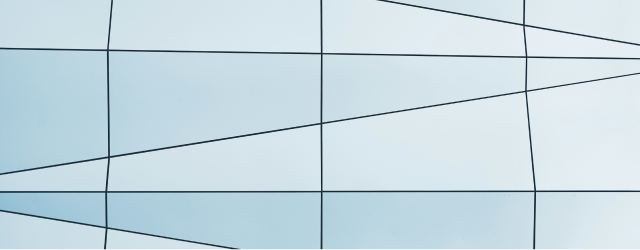
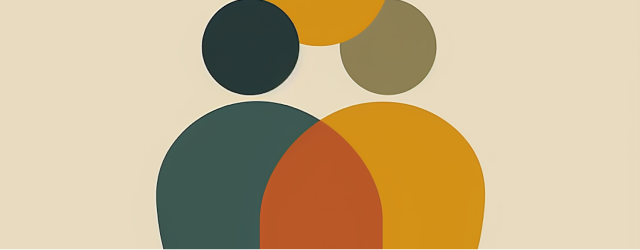