CAD/CAM Software
Gain a thorough understanding of CAD/CAM Software in manufacturing, with insights into their application, benefits, and strategic importance in the industry.
Overview of CAD/CAM Software
CAD/CAM software is a cornerstone of modern manufacturing technology, facilitating the transition from conceptual design to physical production with remarkable precision and efficiency. At its core, CAD involves the creation of detailed 2D or 3D models using computer software, enabling designers to visualize and refine their concepts. These digital models serve as a basis for CAM, which translates the designs into machine instructions, effectively automating the manufacturing process. This synergy between design and production is crucial for maximizing productivity, minimizing errors, and speeding up the development cycle.
The importance of CAD/CAM software cannot be overstated, as it empowers manufacturers to innovate rapidly while maintaining high standards of quality. For instance, in the automotive industry, CAD/CAM tools are used to design complex components such as engine parts, ensuring precision and performance. Similarly, in aerospace, these tools facilitate the creation of intricate geometries required for aircraft components. By providing a digital representation of the physical product, CAD/CAM software enables extensive testing and modification before any material is cut or shaped, reducing waste and saving time.
Moreover, the ability to simulate production processes in a virtual environment allows for the identification and rectification of potential issues before they arise on the shop floor. This proactive approach to design and manufacturing not only enhances efficiency but also contributes to cost reduction, as fewer resources are wasted on trial-and-error methods. As industries continue to embrace digital transformation, CAD/CAM software stands out as a critical enabler of innovation and efficiency.
Role in Manufacturing Efficiency
The integration of CAD/CAM software into manufacturing processes has revolutionized efficiency, providing businesses with the tools necessary to remain competitive. By automating complex design modifications and streamlining production tasks, CAD/CAM software significantly reduces lead times and minimizes material wastage. This is particularly advantageous in industries where time-to-market is a crucial determinant of success.
One of the primary benefits of CAD/CAM software is its ability to support rapid prototyping and customization. In today’s dynamic market environment, consumer preferences are constantly evolving, necessitating swift adaptation from manufacturers. CAD/CAM systems allow for quick alterations to designs, enabling businesses to respond promptly to changing demands. For example, consumer electronics companies often face pressure to release new products with enhanced features. By using CAD/CAM tools, these companies can efficiently modify existing designs to incorporate new technologies or aesthetic elements, ensuring they meet customer expectations.
Furthermore, CAD/CAM software facilitates collaboration across different teams, enhancing communication and coordination within an organization. Real-time updates and shared digital platforms enable engineers, designers, and production managers to work cohesively, reducing the likelihood of errors and discrepancies. This collaborative approach streamlines the entire manufacturing process, from initial design to final production, leading to improved operational efficiency.
In addition to improving internal processes, CAD/CAM software also offers benefits in supplier and customer interactions. By providing detailed digital models, manufacturers can better communicate specifications and requirements to suppliers, ensuring that materials and components meet desired standards. Similarly, customers can visualize and provide feedback on designs before production begins, fostering a more interactive and client-focused approach to manufacturing.
Navigate Manufacturing Project Success with Meegle
Historical development of cad/cam software
Origins of CAD/CAM Software
The origins of CAD/CAM software trace back to the mid-20th century when industries such as aeronautics and automotive sought more efficient ways to design and produce complex components. The initial development of CAD/CAM systems was driven by the need for precision and accuracy, as traditional manual drafting and manufacturing methods were often time-consuming and error-prone. The advent of computing technology provided a solution, enabling the creation of digital models that could be easily modified and replicated.
The first CAD systems emerged in the early 1960s, with the Sketchpad program developed by Ivan Sutherland at MIT being one of the pioneering projects. This groundbreaking software introduced the concept of interactive computer graphics, allowing users to manipulate geometric shapes on a computer screen. Although primitive by today’s standards, Sketchpad laid the foundation for subsequent advancements in CAD technology.
In the following decades, CAD software evolved to include more sophisticated features such as 3D modeling and solid geometry. The introduction of these capabilities marked a significant milestone in the evolution of CAD/CAM software, enabling designers to create more complex and accurate representations of real-world objects. The automotive industry, in particular, played a crucial role in advancing these technologies, as companies sought to improve the design and manufacturing of intricate engine parts and body structures.
Simultaneously, CAM systems were developed to automate the translation of CAD designs into machine instructions. By the 1970s, numerically controlled (NC) machines were being integrated with CAM software, enabling the automated production of complex parts. This integration marked a significant step forward in manufacturing, allowing for greater precision and efficiency in production processes.
Evolution Over Time
Over the years, CAD/CAM software has undergone significant evolution, driven by advancements in computing power, software capabilities, and industry-specific needs. The transition from 2D drafting to 3D modeling marked a transformative phase in the development of these tools, enabling designers to create more accurate and detailed representations of their concepts. This shift not only improved the quality of designs but also facilitated better communication and collaboration among various stakeholders involved in the manufacturing process.
One of the key breakthroughs in CAD/CAM technology was the introduction of parametric modeling. This approach allowed designers to define relationships between different elements of a model, ensuring that any changes made to one part would automatically update related components. This capability greatly enhanced design flexibility and efficiency, as modifications could be made quickly without the need to manually adjust each element.
Another significant advancement was the integration of simulation and analysis tools into CAD/CAM systems. These features enabled designers to test and validate their models in a virtual environment, assessing factors such as stress, strain, and thermal effects. By identifying potential issues before production, manufacturers could minimize the risk of errors and improve product quality. For example, in the aerospace industry, simulation tools are used to analyze the aerodynamic performance of aircraft components, ensuring they meet stringent safety and performance standards.
The rise of cloud computing has further expanded the capabilities of CAD/CAM software, enabling remote access and collaboration across global teams. Cloud-based platforms allow users to store and share large design files, facilitating seamless communication and coordination among geographically dispersed teams. This has been particularly beneficial for multinational companies with design and production facilities in different locations.
Click here to read our expertly curated top picks!
Core principles and techniques
Fundamental Concepts
To fully leverage the potential of CAD/CAM software, it is essential to understand its core principles and concepts. At the heart of these systems lies parametric modeling, a technique that allows designers to create models based on defined parameters and constraints. This approach ensures that any changes made to one part of the model automatically update related components, maintaining design integrity and consistency.
Geometric dimensioning and tolerancing (GD&T) is another critical concept in CAD/CAM. GD&T provides a standardized language for defining the size, shape, and orientation of features within a design. By specifying allowable deviations, GD&T ensures that manufactured parts meet precise quality standards. This is particularly important in industries where tight tolerances are essential, such as aerospace and automotive, where even minor deviations can significantly impact performance and safety.
Tolerance analysis, a complementary concept to GD&T, involves assessing the cumulative effect of dimensional variations on the overall assembly. By analyzing potential sources of variation, designers can identify critical areas that require tighter control, ensuring the final product meets desired specifications. This proactive approach to design and manufacturing helps minimize the risk of defects and rework, enhancing overall efficiency and quality.
Another fundamental principle of CAD/CAM software is the use of 3D modeling, which enables designers to create detailed representations of their concepts. Unlike traditional 2D drafting, 3D modeling provides a more comprehensive view of the design, allowing for better visualization and analysis. This capability is particularly valuable in complex assemblies, where understanding the spatial relationships between different components is crucial.
Implementation Techniques
Implementing CAD/CAM software in a manufacturing environment requires careful planning and execution to maximize its effectiveness. One of the key techniques in this process is feature-based modeling, which involves defining individual features of a part, such as holes, slots, and fillets, as distinct elements within the model. This approach allows for greater flexibility and control over the design, as changes can be made at the feature level without affecting the entire model.
Tool path generation is another essential technique in CAD/CAM implementation. This process involves creating the instructions that guide CNC machines in shaping the material according to the design. By optimizing tool paths, manufacturers can reduce machining time and improve surface finish, enhancing overall efficiency and quality. Advanced CAM software offers features such as automatic tool path optimization, which analyzes various factors such as material properties and machine capabilities to generate the most efficient machining strategy.
Post-processing, the final step in the CAD/CAM workflow, involves converting the tool paths into machine-specific code that can be executed by CNC equipment. This step is crucial for ensuring compatibility between the software and the hardware, as different machines may require different codes and formats. By customizing post-processing settings, manufacturers can ensure seamless communication between the CAD/CAM system and the production equipment, minimizing the risk of errors and delays.
Effective implementation of CAD/CAM software also requires a focus on training and skill development. As these systems become more advanced, the need for skilled operators who can navigate and utilize their features effectively becomes paramount. Investing in training programs and workshops ensures that employees are well-equipped to handle the complexities of CAD/CAM software, maximizing its potential benefits.
Benefits and challenges
Advantages in Production
The adoption of CAD/CAM software in manufacturing brings a multitude of advantages, significantly enhancing production efficiency and product quality. One of the most notable benefits is the improved accuracy and precision in design and manufacturing processes. By providing detailed digital models and automated machining instructions, CAD/CAM software minimizes the risk of errors and ensures that final products meet exact specifications.
In addition to enhancing accuracy, CAD/CAM systems contribute to cost reduction by streamlining production workflows and minimizing material wastage. Automated processes eliminate the need for manual interventions, reducing labor costs and freeing up resources for other critical tasks. Moreover, the ability to simulate and validate designs in a virtual environment allows for early identification of potential issues, preventing costly rework and scrap.
The accelerated time-to-market is another significant advantage of CAD/CAM software. In today’s fast-paced market, the ability to bring new products to market quickly can be a key competitive differentiator. CAD/CAM systems enable rapid prototyping and design iterations, allowing manufacturers to respond swiftly to changing customer demands and market trends. For instance, consumer electronics companies often rely on CAD/CAM tools to expedite the development of new devices, ensuring they stay ahead of competitors in a rapidly evolving industry.
Furthermore, CAD/CAM software facilitates real-time collaboration among different teams, enhancing communication and coordination within an organization. By providing a shared digital platform, designers, engineers, and production managers can work together seamlessly, reducing the likelihood of errors and discrepancies. This collaborative approach not only improves internal processes but also enhances interactions with suppliers and customers, fostering stronger relationships and better outcomes.
Potential Limitations
Despite its numerous benefits, the implementation of CAD/CAM software in manufacturing is not without challenges. One of the primary limitations is the high initial cost associated with acquiring and integrating these systems. The investment in CAD/CAM software, along with the necessary hardware and training, can be substantial, particularly for small and medium-sized enterprises (SMEs) with limited budgets. However, considering the long-term benefits, many manufacturers view this as a worthwhile investment.
Another challenge is the complexity of CAD/CAM systems, which can pose difficulties for operators who are unfamiliar with their features and functionalities. The continuous evolution of these tools necessitates ongoing training and skill development to ensure users remain proficient. Organizations must invest in training programs and resources to equip employees with the necessary knowledge and skills to navigate and utilize CAD/CAM software effectively.
Additionally, the integration of CAD/CAM systems with existing manufacturing infrastructure can be complex and time-consuming. Ensuring compatibility between software and hardware, as well as aligning workflows, requires careful planning and execution. Manufacturers must collaborate with software vendors and technical experts to ensure seamless integration and minimize disruptions to production.
Addressing these challenges requires a strategic approach, including careful assessment of organizational needs, selection of appropriate software, and investment in training and support. By proactively managing these issues, manufacturers can fully harness the capabilities of CAD/CAM software, maximizing its benefits and minimizing potential drawbacks.
Click here to read our expertly curated top picks!
Case studies and real-world applications
Industry examples
Industry examples
CAD/CAM software has found applications across diverse industries, revolutionizing design and manufacturing processes with its advanced capabilities. In the automotive sector, for example, these tools are instrumental in the design and production of complex components such as engine parts, transmissions, and chassis. By leveraging CAD/CAM systems, automotive manufacturers can achieve precise geometries and tight tolerances, ensuring optimal performance and reliability.
One notable example is General Motors, which has successfully integrated CAD/CAM software into its design and manufacturing workflows. By utilizing these tools, the company has streamlined its production processes, reducing lead times and minimizing material wastage. The ability to simulate and validate designs in a virtual environment has also enabled GM to enhance product quality and innovation, maintaining its competitive edge in the automotive industry.
In the aerospace industry, CAD/CAM software plays a crucial role in the design and manufacture of aircraft components. Given the stringent safety and performance standards in this sector, precision and accuracy are paramount. CAD/CAM systems facilitate the creation of intricate geometries required for aircraft structures, enabling manufacturers to meet stringent regulatory requirements. Boeing, a leading aerospace company, leverages CAD/CAM tools to design and produce components for its commercial and military aircraft, ensuring they meet the highest standards of quality and performance.
The medical device industry has also benefited from the adoption of CAD/CAM software, particularly in the design and manufacture of custom implants and prosthetics. These tools enable the creation of patient-specific models, ensuring a perfect fit and optimal functionality. By integrating CAD/CAM systems into their workflows, medical device manufacturers can enhance efficiency and precision, improving patient outcomes and satisfaction.
Impact analysis
Impact analysis
The impact of CAD/CAM software on manufacturing processes is profound, resulting in tangible improvements in efficiency, sustainability, and innovation. One of the most significant effects is the reduction in production costs, achieved through streamlined workflows and minimized material wastage. By automating design and manufacturing processes, CAD/CAM systems eliminate the need for costly manual interventions, reducing labor costs and enhancing resource allocation.
The ability to simulate and validate designs in a virtual environment has also contributed to improved product quality and reduced defect rates. By identifying and addressing potential issues before production begins, manufacturers can minimize the risk of errors and rework. This proactive approach not only enhances product reliability but also boosts customer satisfaction and loyalty.
CAD/CAM software has also played a pivotal role in advancing sustainability efforts within the manufacturing sector. By optimizing material usage and reducing waste, these systems contribute to more environmentally friendly production processes. Additionally, the ability to design and produce lightweight components, particularly in industries such as automotive and aerospace, leads to reduced energy consumption and emissions, aligning with global sustainability goals.
Innovation is another key area where CAD/CAM software has made a significant impact. By enabling rapid prototyping and design iterations, these tools facilitate the development of innovative products that meet evolving market demands. The ability to experiment with new materials and geometries in a digital environment encourages creativity and exploration, driving continuous improvement and growth.
Technological integration and innovations
Current Technologies
CAD/CAM software has evolved to integrate seamlessly with cutting-edge technologies such as artificial intelligence (AI), machine learning (ML), and the Internet of Things (IoT). These integrations enhance design automation, predictive maintenance, and adaptive production, elevating the capabilities of CAD/CAM systems to new heights. AI and ML, for example, are used to automate routine tasks, such as tool path optimization and defect detection, freeing up valuable resources for more complex and creative projects.
The integration of IoT technology has also transformed the manufacturing landscape, enabling real-time data collection and analysis. By connecting machines, sensors, and systems, manufacturers can monitor production processes, identify inefficiencies, and implement corrective actions promptly. This connectivity enhances decision-making and fosters a more agile and responsive manufacturing environment.
Cloud computing has further expanded the capabilities of CAD/CAM software, offering remote access and collaboration across global teams. Cloud-based platforms allow users to store and share large design files, facilitating seamless communication and coordination among geographically dispersed teams. This has been particularly beneficial for multinational companies with design and production facilities in different locations, ensuring consistency and alignment across the organization.
Future Trends
Looking ahead, several emerging trends are poised to shape the future of CAD/CAM technology, offering unprecedented opportunities for innovation and efficiency. One such trend is the adoption of cloud computing, which promises to further streamline design and production processes. By providing scalable and flexible solutions, cloud-based CAD/CAM platforms enable manufacturers to access advanced tools and resources without the need for significant upfront investments.
Augmented reality (AR) is another emerging trend that holds great potential for CAD/CAM applications. By overlaying digital information onto the physical world, AR enhances visualization and interaction, enabling designers to review and modify models in a more intuitive and immersive manner. This technology is particularly valuable in complex assembly and maintenance tasks, where real-time guidance and feedback can improve accuracy and efficiency.
Additive manufacturing, or 3D printing, is also transforming the manufacturing landscape, offering new possibilities for design and production. By enabling the creation of complex geometries and customized parts, additive manufacturing complements CAD/CAM systems, expanding their capabilities and applications. The integration of these technologies promises to revolutionize industries such as aerospace, automotive, and healthcare, offering unprecedented flexibility and precision.
Click here to read our expertly curated top picks!
Tips for do's and dont's
Do's | Dont's |
---|---|
Invest in training and skill development for your team. | Don't overlook the importance of regular software updates. |
Customize workflows to align with your specific manufacturing needs. | Avoid rushing the integration process without thorough planning. |
Keep abreast of the latest industry trends and software advancements. | Don't neglect the importance of cybersecurity measures. |
Collaborate with software vendors to optimize system capabilities. | Avoid underestimating the complexity of CAD/CAM systems. |
Click here to read our expertly curated top picks!
Conclusion
Summary of Key Points
Throughout this comprehensive exploration of CAD/CAM software, we have delved into its transformative impact on modern manufacturing, highlighting its crucial role in enhancing efficiency and driving innovation. From its origins in the mid-20th century to its current applications across diverse industries, CAD/CAM technology has revolutionized design and production processes, offering unprecedented precision and flexibility. The synergy between CAD and CAM enables seamless transitions from design to manufacturing, minimizing errors and optimizing workflows. By leveraging these powerful tools, manufacturers can reduce costs, accelerate time-to-market, and improve product quality, maintaining a competitive edge in today’s dynamic market environment.
Encouraging Ongoing Adaptation
As the manufacturing landscape continues to evolve, it is imperative for professionals to stay informed about the latest advancements in CAD/CAM technology. By embracing continuous learning and adaptation, businesses can fully harness the capabilities of these systems, driving growth and innovation. Proactively investing in training and skill development ensures that employees remain proficient in navigating and utilizing CAD/CAM tools effectively. Moreover, staying abreast of emerging trends and technologies, such as cloud computing, augmented reality, and additive manufacturing, can unlock new opportunities and applications, further enhancing operational efficiency and competitiveness. In a rapidly changing world, ongoing adaptation and integration of CAD/CAM software are key to maintaining a competitive edge and achieving long-term success.
Navigate Manufacturing Project Success with Meegle
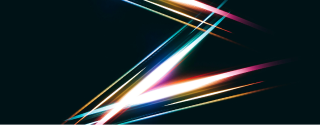
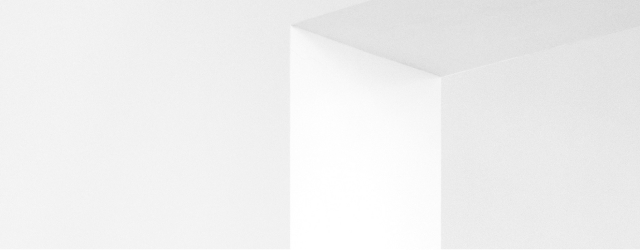
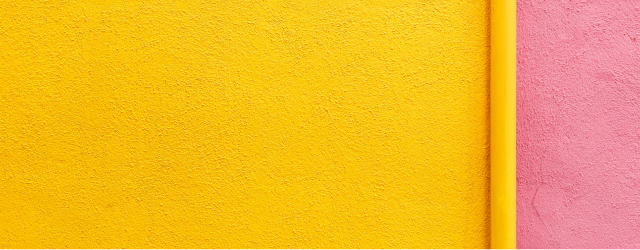
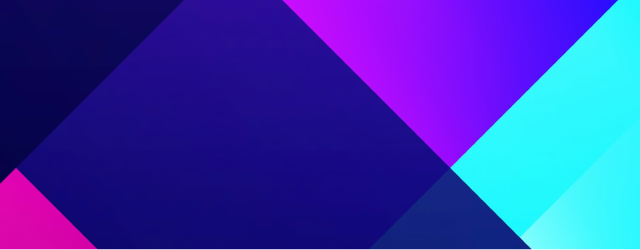
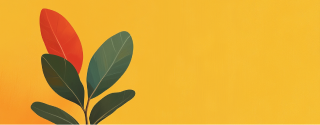
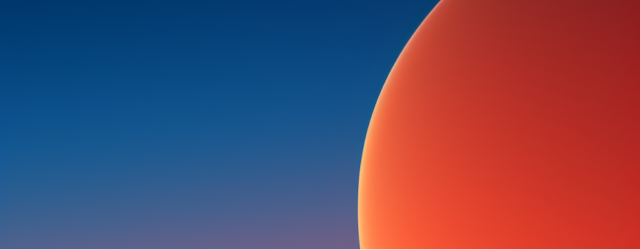
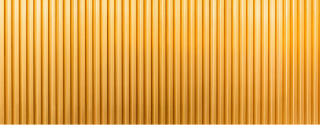
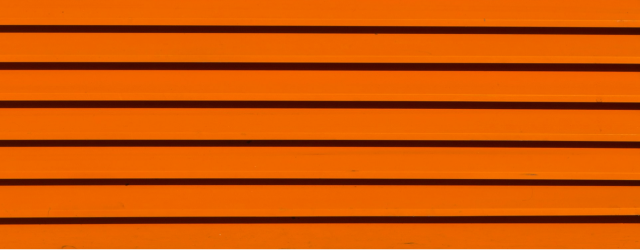