Capacity Utilization
Gain a thorough understanding of Capacity Utilization in manufacturing, with insights into their application, benefits, and strategic importance in the industry.
Overview of Capacity Utilization
Capacity utilization is a crucial concept in manufacturing that reflects the proportion of potential output being used at any given time. Typically expressed as a percentage, it signifies the extent to which a company's production capabilities are being employed. For instance, if a factory has a production capacity of 100 units but is only producing 70 units, its capacity utilization rate stands at 70%. This metric is essential because it provides insights into whether a company is efficiently using its resources or if there’s room for improvement.
Understanding capacity utilization is integral for several reasons. First, it directly influences operational costs. Higher capacity utilization often leads to lower per-unit costs as fixed expenses are spread over more units of output. Second, it impacts competitiveness. Companies that utilize their capacity effectively are better positioned to respond to market demands, produce goods at a lower cost, and offer more competitive pricing. Lastly, it affects productivity. Optimizing capacity utilization can lead to improved workflows, reduced waste, and enhanced product quality.
For manufacturing professionals, grasping the nuances of capacity utilization can unlock the potential for significant operational improvements. By analyzing production data and identifying inefficiencies, they can develop strategies to enhance capacity utilization, ultimately leading to higher productivity and profitability.
Role in Manufacturing Efficiency
Capacity utilization is a direct indicator of manufacturing efficiency, reflecting how well a company leverages its resources to produce goods. When companies achieve high capacity utilization, they often see improvements in product quality, waste reduction, and streamlined processes. A pivotal aspect of manufacturing efficiency is the ability to produce more with less—less time, less cost, and less waste.
For example, consider a manufacturing plant that produces automotive parts. By analyzing its capacity utilization, the plant can identify bottlenecks in its production line, such as machinery downtime or inefficient scheduling. Addressing these issues can lead to improved throughput, reduced lead times, and enhanced product quality. Additionally, high capacity utilization often correlates with increased employee satisfaction. Workers tend to be more engaged and productive when operations are smooth and efficient.
Moreover, capacity utilization helps manufacturers forecast demand and plan production schedules effectively. By understanding utilization rates, companies can adjust their operations to prevent overproduction and underproduction, minimizing inventory costs and aligning production with market needs.
Overall, capacity utilization is not merely a metric but a potent strategic tool that manufacturers can harness to achieve excellence in their operations. It provides a clear lens through which organizations can view their efficiency and make informed decisions to enhance their competitiveness in the manufacturing landscape.
Navigate Manufacturing Project Success with Meegle
Historical development of capacity utilization
Origins of Capacity Utilization
The concept of capacity utilization has roots in early industrial practices, where maximizing production efficiency was a critical concern. During the Industrial Revolution, manufacturers began to recognize the importance of utilizing machinery and labor optimally to increase output and profitability. This era marked the beginning of organized efforts to measure and improve capacity utilization.
In the early 20th century, capacity utilization evolved as manufacturing processes became more complex and data-driven. The introduction of scientific management principles by Frederick Taylor emphasized the need for systematic analysis of production capabilities and efficiency. Manufacturers started using standardized metrics to assess their production capacity, laying the groundwork for modern capacity utilization practices.
A historical case study that exemplifies the early adoption of capacity utilization is the Ford Motor Company's assembly line innovation. By streamlining production processes and optimizing capacity utilization, Ford significantly reduced the time and cost of manufacturing automobiles, revolutionizing the industry. This approach not only increased output but also set a precedent for other manufacturers to follow.
Today, capacity utilization has become a formalized metric, integral to operational decision-making in manufacturing. Understanding its historical origins provides valuable context for its current applications and highlights the importance of continuous improvement in capacity management.
Evolution Over Time
The landscape of capacity utilization has undergone significant transformations, largely driven by technological advancements and methodological innovations. In the mid-20th century, the advent of automation and computerized control systems revolutionized capacity management, enabling manufacturers to monitor and optimize production processes with unprecedented precision.
The introduction of data analytics further enhanced capacity utilization strategies. Manufacturers began leveraging data to gain insights into production patterns, identify inefficiencies, and predict demand fluctuations. This shift marked a transition from reactive to proactive capacity management, allowing companies to make informed decisions based on real-time data.
Another key development in capacity utilization is the adoption of lean manufacturing principles. Lean methodologies focus on minimizing waste and maximizing value, aligning perfectly with the goals of capacity utilization. Techniques such as Just-In-Time (JIT) production and continuous improvement (Kaizen) have become integral to optimizing capacity utilization and achieving manufacturing excellence.
Today, manufacturers are increasingly integrating advanced technologies such as artificial intelligence (AI) and the Internet of Things (IoT) to enhance capacity utilization. These technologies enable real-time monitoring, predictive maintenance, and automated decision-making, further optimizing production processes.
As capacity utilization continues to evolve, manufacturers must stay abreast of technological advancements and methodological innovations to maintain their competitiveness and achieve sustainable growth.
Click here to read our expertly curated top picks!
Core principles and techniques
Fundamental Concepts
Understanding the fundamental concepts of capacity utilization is essential for effective implementation in manufacturing environments. Capacity utilization is calculated by dividing the actual production output by the maximum potential output, expressed as a percentage. This calculation provides insights into how efficiently a company is utilizing its production capabilities.
A key distinction in capacity utilization is between theoretical capacity and practical capacity. Theoretical capacity represents the maximum output a facility can achieve under ideal conditions, while practical capacity accounts for real-world factors such as equipment downtime, maintenance, and labor constraints. Manufacturers must balance these two capacities to develop realistic utilization strategies.
Another fundamental concept is capacity constraints. These are factors that limit the ability to achieve full capacity utilization, such as bottlenecks in production processes or resource limitations. Identifying and addressing capacity constraints is crucial for optimizing utilization rates and enhancing productivity.
Capacity utilization also involves understanding the demand-capacity balance. Manufacturers must align their production capabilities with market demand to prevent overproduction or underproduction. This balance ensures efficient resource allocation and minimizes inventory costs.
By grasping these fundamental concepts, manufacturing professionals can develop strategies to optimize capacity utilization, enhance productivity, and achieve operational excellence.
Implementation Techniques
Implementing capacity utilization strategies requires a suite of techniques tailored to specific manufacturing environments. One effective technique is scheduling optimization, which involves aligning production schedules with demand forecasts to maximize capacity utilization. By optimizing scheduling, manufacturers can reduce downtime, minimize inventory costs, and improve workflow efficiency.
Another key technique is bottleneck analysis. Identifying bottlenecks in production processes allows manufacturers to address constraints and enhance throughput. Techniques such as process reengineering and resource allocation can help eliminate bottlenecks and improve capacity utilization.
Lean manufacturing principles also play a crucial role in capacity utilization. Techniques such as Just-In-Time (JIT) production and continuous improvement (Kaizen) focus on minimizing waste and maximizing value, aligning perfectly with the goals of capacity utilization. Implementing lean methodologies can lead to significant improvements in efficiency and productivity.
Advanced technologies such as AI and IoT are increasingly being used to enhance capacity utilization. These technologies enable real-time monitoring, predictive maintenance, and automated decision-making, further optimizing production processes. By integrating technology into capacity utilization strategies, manufacturers can achieve more sophisticated and effective utilization.
Overall, implementing capacity utilization techniques requires a strategic approach that considers the unique needs and constraints of each manufacturing environment. By adopting best practices and leveraging technology, manufacturers can optimize capacity utilization and achieve sustainable growth.
Benefits and challenges
Advantages in Production
Capacity utilization offers numerous benefits to manufacturing processes, enhancing efficiency and competitiveness. One of the primary advantages is increased output. By optimizing utilization rates, manufacturers can produce more goods with the same resources, increasing overall productivity and profitability.
Another significant benefit is enhanced product quality. High capacity utilization often correlates with reduced waste and improved workflow efficiency, leading to higher-quality products. This improvement in product quality can result in increased customer satisfaction and loyalty, further boosting competitive positioning.
Effective capacity utilization also leads to cost savings. By maximizing the use of installed equipment and facilities, manufacturers can reduce per-unit costs and increase profit margins. Additionally, aligning production capabilities with market demand can minimize inventory costs and enhance resource allocation.
A practical example of these advantages can be seen in the consumer goods industry. By implementing strategic capacity utilization techniques, manufacturers can optimize their production processes, reduce lead times, and improve supply chain efficiency. This optimization results in higher output, better product quality, and significant cost savings.
Overall, capacity utilization is a powerful tool for enhancing manufacturing efficiency and achieving competitive advantage. By leveraging its benefits, manufacturers can drive growth, improve profitability, and ensure sustainable operations.
Potential Limitations
Despite its benefits, capacity utilization is not without its challenges. One potential limitation is the risk of over-utilization. Pushing systems to their maximum capacity can lead to resource strain, increased wear and tear on equipment, and reduced employee morale. Manufacturers must balance utilization rates to prevent over-utilization and ensure sustainable operations.
Another challenge is the impact of unforeseen disruptions. Factors such as equipment breakdowns, supply chain interruptions, and demand fluctuations can affect capacity utilization rates and disrupt production processes. Manufacturers must develop contingency plans to mitigate these disruptions and maintain operational efficiency.
Additionally, capacity utilization requires a deep understanding of demand-capacity balance. Aligning production capabilities with market demand can be challenging, especially in industries with fluctuating demand patterns. Manufacturers must continuously monitor market trends and adjust their operations to prevent overproduction or underproduction.
To overcome these challenges, manufacturers can implement strategic solutions such as predictive maintenance, flexible scheduling, and scenario planning. By adopting a proactive approach to capacity management, companies can mitigate limitations and ensure sustainable growth.
Overall, while capacity utilization offers numerous benefits, manufacturers must address its challenges to achieve optimal results and maintain competitiveness in the manufacturing landscape.
Click here to read our expertly curated top picks!
Case studies and real-world applications
Industry examples
Industry examples
Real-world examples provide valuable insights into successful capacity utilization strategies across various industries. In the automotive sector, Toyota's implementation of lean manufacturing principles has become a benchmark for capacity optimization. By focusing on continuous improvement and waste reduction, Toyota has achieved high capacity utilization rates, resulting in increased efficiency and product quality.
In the consumer goods industry, Procter & Gamble (P&G) has successfully leveraged capacity utilization strategies to enhance supply chain efficiency. By aligning production schedules with demand forecasts, P&G has reduced lead times and minimized inventory costs, achieving significant cost savings and improved customer satisfaction.
Another notable example is the electronics industry, where companies like Samsung have integrated advanced technologies to optimize capacity utilization. By utilizing IoT and AI for real-time monitoring and predictive maintenance, Samsung has enhanced production processes and achieved higher utilization rates, resulting in increased output and profitability.
These industry examples highlight diverse approaches to capacity utilization, showcasing the potential for significant improvements in efficiency and competitiveness. By learning from successful case studies, manufacturers can develop strategies to optimize their own capacity utilization and achieve sustainable growth.
Impact analysis
Impact analysis
Analyzing the impact of capacity utilization in real-world scenarios provides insights into measurable improvements achieved through effective strategies. One tangible impact is increased throughput. By optimizing capacity utilization, manufacturers can produce more goods with the same resources, resulting in higher output and profitability.
Another significant impact is reduced lead times. Efficient capacity management allows manufacturers to streamline production processes, minimize downtime, and accelerate delivery schedules. This reduction in lead times enhances customer satisfaction and strengthens competitive positioning.
Effective capacity utilization also leads to enhanced profitability. By maximizing the use of installed equipment and facilities, manufacturers can reduce per-unit costs and increase profit margins. Additionally, aligning production capabilities with market demand can minimize inventory costs and optimize resource allocation, contributing to overall profitability.
In the manufacturing industry, these impacts are evident in companies that have successfully implemented capacity utilization strategies. For example, by integrating advanced technologies and lean methodologies, manufacturers can achieve significant improvements in efficiency, product quality, and cost savings.
Technological integration and innovations
Current Technologies
The integration of technology is pivotal to advancing capacity utilization efforts in modern manufacturing environments. One key technology is the Internet of Things (IoT), which enables real-time monitoring and control of production processes. By collecting and analyzing data from connected devices, manufacturers can optimize capacity utilization, enhance workflow efficiency, and reduce downtime.
Artificial Intelligence (AI) is another transformative technology that plays a significant role in capacity utilization. AI algorithms can analyze production data, predict demand patterns, and automate decision-making, leading to improved utilization rates and enhanced productivity. Additionally, AI-powered predictive maintenance can reduce equipment downtime and extend asset lifespan, contributing to sustainable operations.
Advanced manufacturing systems, such as enterprise resource planning (ERP) software, also enhance capacity utilization. These systems provide integrated solutions for managing production schedules, inventory, and resource allocation, enabling manufacturers to optimize capacity utilization and achieve operational excellence.
Overall, current technologies offer significant potential for enhancing capacity utilization and driving growth in the manufacturing sector. By leveraging these technologies, manufacturers can achieve more sophisticated and effective utilization strategies, ensuring competitiveness and sustainability.
Future Trends
Staying ahead of future trends is crucial for maintaining a competitive advantage in capacity utilization. One emerging trend is the rise of smart factories, characterized by interconnected systems and automated processes. Smart factories leverage advanced technologies such as IoT, AI, and robotics to optimize capacity utilization, enhance production efficiency, and reduce costs.
Another future trend is the integration of advanced analytics in capacity utilization strategies. By utilizing big data and machine learning algorithms, manufacturers can gain deeper insights into production patterns, identify inefficiencies, and predict demand fluctuations. This shift towards data-driven decision-making enables companies to achieve higher utilization rates and improve operational performance.
The adoption of sustainable manufacturing practices is also gaining traction in capacity utilization. Manufacturers are increasingly focusing on reducing waste, minimizing energy consumption, and optimizing resource allocation to achieve sustainability goals. By aligning capacity utilization strategies with environmental considerations, companies can enhance their competitive positioning and meet regulatory requirements.
Overall, future trends in capacity utilization offer significant opportunities for innovation and growth in the manufacturing sector. By staying abreast of these developments, manufacturers can prepare for upcoming shifts and maintain competitiveness in the ever-evolving landscape.
Click here to read our expertly curated top picks!
Capacity utilization: do's and don'ts
Creating a balanced approach to capacity utilization is crucial for achieving sustainable growth and maintaining competitiveness. The following table presents a practical guide on the do's and don'ts of capacity utilization, offering clear guidelines for manufacturing professionals.
Do's | Don'ts |
---|---|
Regularly assess and recalibrate capacity plans | Avoid over-reliance on outdated capacity data |
Invest in technology for real-time monitoring | Ignore the impact of external market changes |
Train staff on new processes and technologies | Overlook the importance of maintenance |
Focus on sustainable and scalable strategies | Push systems to over-capacity frequently |
Click here to read our expertly curated top picks!
Conclusion
Summary of Key Points
In conclusion, capacity utilization is a vital metric in the manufacturing industry, reflecting the extent to which production capabilities are being utilized. By optimizing utilization rates, manufacturers can achieve higher output, enhanced product quality, and significant cost savings. The historical development of capacity utilization highlights its evolution from early industrial practices to modern methodologies driven by technological advancements. Core principles, such as the distinction between theoretical and practical capacity, underpin effective implementation, while strategic techniques, such as scheduling optimization and bottleneck analysis, enhance utilization rates. Despite its benefits, capacity utilization presents challenges, such as over-utilization and unforeseen disruptions, requiring proactive solutions. Technological integration and future trends offer significant opportunities for innovation, driving growth and ensuring competitiveness. By adhering to best practices and leveraging technology, manufacturers can sustain optimal capacity utilization and achieve sustainable operations.
Encouraging Ongoing Adaptation
As the manufacturing landscape continues to evolve, professionals must stay updated and consider integrating capacity utilization into their strategies for enhanced outcomes. Ongoing adaptation and innovation are crucial for maintaining competitiveness in the ever-changing environment. By embracing technological advancements, strategic planning, and continuous improvement initiatives, manufacturers can optimize capacity utilization and achieve sustainable growth. Encouraging a culture of adaptation and innovation ensures resilience and success in the dynamic manufacturing industry.
Navigate Manufacturing Project Success with Meegle
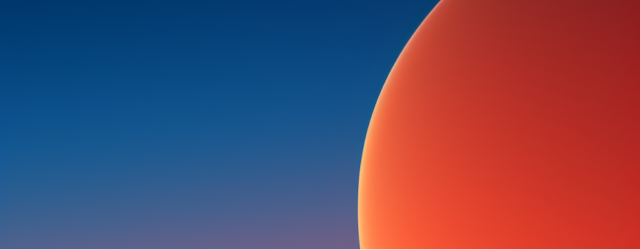
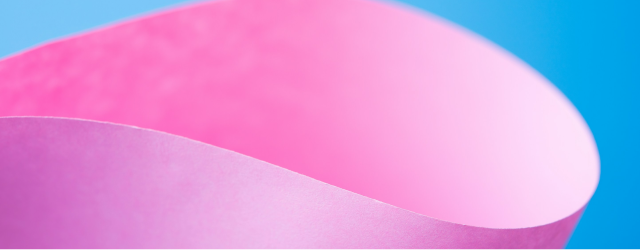
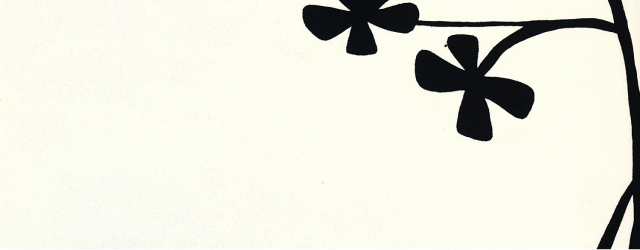
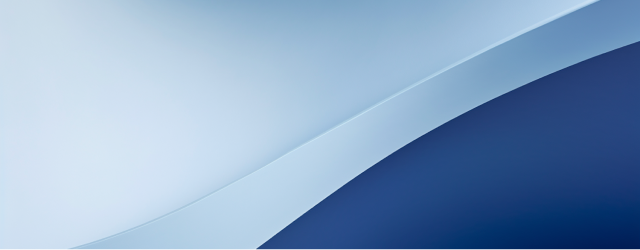
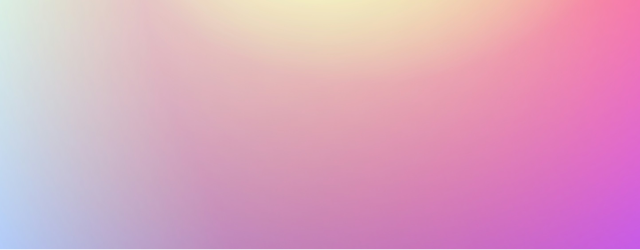
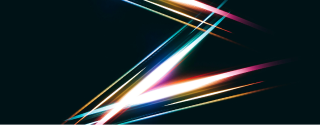
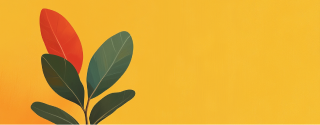
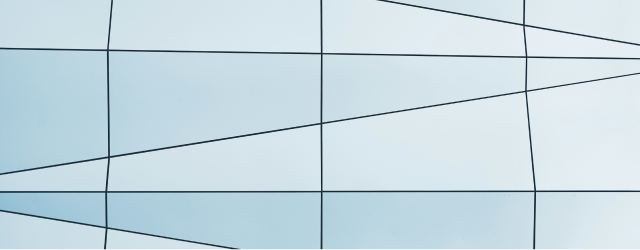