Casting Technologies
Gain a thorough understanding of Casting Technologies in manufacturing, with insights into their application, benefits, and strategic importance in the industry.
Overview of Casting Technologies
Casting technologies are foundational to manufacturing, enabling the creation of diverse shapes from molten materials. The process involves pouring liquid metal into molds, where it cools and solidifies into the desired form. This technique is pivotal in industries like automotive and aerospace, where precision and durability are crucial. From engine blocks to intricate turbine blades, casting technologies facilitate the production of components adhering to stringent specifications. The versatility of casting processes allows for the fabrication of parts with complex geometries that would be challenging to achieve through other manufacturing methods. In modern contexts, advances such as investment casting and die casting offer enhanced capabilities, making casting indispensable in high-performance applications.
Role in Manufacturing Efficiency
Integrating casting technologies into manufacturing workflows enhances both efficiency and quality. By enabling precise formation of intricate designs, casting minimizes material waste and reduces the need for additional machining. For instance, in the automotive industry, casting allows for the streamlined production of high-strength components with minimal material usage, significantly cutting costs. The reduction in machining not only saves time but also diminishes wear and tear on equipment, further optimizing operational efficiency. Additionally, the ability to produce complex shapes in a single step accelerates production timelines, allowing manufacturers to meet market demands swiftly. The resultant cost savings and quality improvements underscore the critical role of casting technologies in achieving competitive advantage.
Navigate Manufacturing Project Success with Meegle
Historical development of casting technologies
Origins of Casting Technologies
The origins of casting technologies trace back to ancient civilizations, where artisans began shaping metals through rudimentary casting techniques. Early examples include the use of clay molds to cast bronze weapons and tools, a testament to the ingenuity of early craftsmen. As societies evolved, so did casting methods, driven by the need for durable and precise metalwork. The Industrial Revolution marked a turning point, introducing mechanized processes that expanded casting's application beyond artisanal crafts to large-scale manufacturing. This historical journey reveals how casting has been instrumental in driving technological advancements and shaping the course of industrial production.
Evolution Over Time
Over centuries, casting technologies have undergone significant transformations, evolving from basic sand casting to sophisticated methods like investment casting and centrifugal casting. These advancements have been fueled by technological progress and changing industrial demands. Investment casting, for example, involves creating a wax model encased in ceramic material, offering unparalleled precision for complex geometries. Similarly, centrifugal casting utilizes rotational force to distribute molten metal evenly within molds, enhancing material properties. These innovations reflect the continuous quest for efficiency and precision in manufacturing, highlighting the adaptability of casting technologies to meet evolving production needs.
Click here to read our expertly curated top picks!
Core principles and techniques
Fundamental Concepts
To leverage casting technologies effectively, understanding fundamental principles is crucial. Key concepts include mold design, material selection, and thermal dynamics, which collectively influence casting outcomes. Mold design must account for factors like shrinkage and cooling rates to ensure dimensional accuracy. Material selection is equally critical, as different alloys offer varying properties conducive to specific applications. Thermal dynamics, encompassing heat transfer and solidification, dictate the quality of the cast product. Mastery of these principles provides manufacturers with the expertise to navigate casting processes, optimize conditions, and achieve desired results in component fabrication.
Implementation Techniques
The application of casting technologies involves a variety of techniques tailored to specific materials and component designs. Among these, die casting, centrifugal casting, and continuous casting are prominent. Die casting, ideal for mass production, uses high-pressure to inject molten metal into reusable molds, ensuring consistent product quality. Centrifugal casting is advantageous for cylindrical shapes, producing materials with superior mechanical properties. Continuous casting, often used in metallurgy, allows for the uninterrupted production of long metal sections. Each technique offers distinct benefits and use cases, empowering professionals to select methods that align with their manufacturing goals.
Benefits and challenges
Advantages in Production
Casting technologies offer a multitude of advantages that can transform manufacturing processes. Key benefits include cost savings, design flexibility, and the ability to produce complex geometries with high precision. For example, the streamlined nature of casting reduces the need for extensive machining, resulting in lower production costs. Design flexibility allows for the creation of intricate parts that would be difficult to achieve through other methods, enhancing innovation potential. Moreover, the precision inherent in casting processes ensures uniform material properties, improving component reliability and performance. By capitalizing on these strengths, manufacturers can achieve strategic objectives and operational improvements.
Potential Limitations
Despite their benefits, casting technologies also present challenges that require careful management. Common limitations include issues with dimensional accuracy and material constraints. Achieving precise dimensions can be difficult due to factors like mold shrinkage and thermal expansion. Additionally, not all materials are suitable for casting, with some alloys presenting challenges in terms of fluidity and cooling rates. To overcome these hurdles, manufacturers must implement rigorous process controls, invest in advanced equipment, and adopt innovative design strategies. By proactively addressing these challenges, professionals can ensure successful casting operations and maximize the efficacy of their manufacturing processes.
Click here to read our expertly curated top picks!
Case studies and real-world applications
Industry examples
Industry examples
Real-world examples offer invaluable insights into the practical application of casting technologies across various sectors. These case studies highlight how industries have successfully integrated casting into their manufacturing processes, illustrating the tangible benefits achieved.
Example 1: Automotive Industry
In the automotive industry, casting technologies are pivotal for producing engine parts, transmission components, and structural elements. Leading manufacturers utilize casting to enhance component durability and reduce production costs. For instance, aluminum die casting is frequently employed to create lightweight yet strong engine blocks, improving fuel efficiency and vehicle performance. This integration of casting techniques has revolutionized automotive design, enabling the production of high-quality components that meet stringent industry standards.
Example 2: Aerospace Manufacturing
In aerospace manufacturing, precision and reliability are paramount, making casting technologies indispensable. Aerospace companies use advanced casting techniques to produce lightweight yet robust components, ensuring safety and efficiency in aircraft design and operation. Investment casting is often employed to manufacture turbine blades, where precision in geometry and material properties is critical for performance. This application underscores the role of casting in achieving the high standards required for aerospace components, demonstrating its impact on industry innovation.
Example 3: Medical Device Production
Casting technologies also play a crucial role in medical device production, where intricate designs and biocompatibility are essential. Medical device manufacturers employ casting to create complex prosthetics and implants, improving patient outcomes through innovation in material science. For example, titanium casting provides the strength and biocompatibility necessary for orthopedic implants, enhancing patient recovery and comfort. This application highlights the transformative potential of casting in advancing healthcare technology, underscoring its importance in medical manufacturing.
Technological integration and innovations
Current Technologies
The synergy between casting technologies and other advancements is driving innovation in manufacturing. Current technologies enhancing casting processes include 3D printing for mold creation and AI for process optimization. 3D printing allows for rapid prototyping and customization of molds, facilitating the production of complex designs with precision. AI applications in casting optimize process parameters, ensuring consistency and quality in output. These integrated solutions empower manufacturers to refine operations, leveraging cutting-edge tools to enhance efficiency and product quality.
Future Trends
The future of casting technologies is poised for exciting developments, shaped by emerging trends and innovations. Anticipated advancements include the adoption of smart materials and the rise of automated casting systems. Smart materials, capable of responding to environmental changes, offer potential for enhanced casting applications in dynamic fields like aerospace and automotive. Automated systems promise increased efficiency and precision, reducing human error and streamlining production workflows. By staying informed of these trends, manufacturers can anticipate shifts and prepare for next-generation casting solutions, positioning their operations for continued success.
Click here to read our expertly curated top picks!
Tips for do's and don'ts in casting technologies
Do's | Don'ts |
---|---|
Ensure thorough mold design | Neglect mold maintenance |
Optimize material selection | Overlook temperature control |
Implement process monitoring | Ignore feedback and data analysis |
Invest in technology upgrades | Rely solely on traditional methods |
Train personnel on best practices | Disregard safety protocols |
Click here to read our expertly curated top picks!
Conclusion
Summary of Key Points
Casting technologies are pivotal in modern manufacturing, offering a blend of precision, efficiency, and versatility. They enable the creation of complex geometries with reduced material waste, enhancing both cost-effectiveness and product quality. By understanding the historical development, core principles, and practical applications of casting, manufacturers can leverage these technologies to achieve strategic objectives. The synergy between casting and other advancements continues to drive innovation, positioning casting as a cornerstone of modern industrial processes.
Encouraging Ongoing Adaptation
As manufacturing continues to evolve, embracing casting technologies and staying abreast of innovations is crucial for maintaining competitive advantage. Professionals are encouraged to integrate casting into their strategic planning, fostering a culture of continuous improvement and adaptation. By embracing change and innovation, manufacturers can unlock new opportunities and drive industry progress, ensuring their operations remain at the forefront of technological advancements.
Navigate Manufacturing Project Success with Meegle
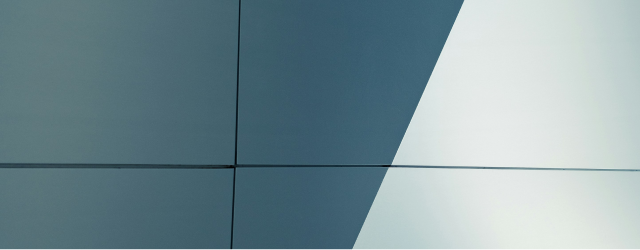
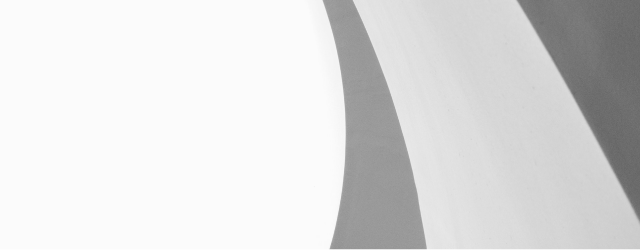
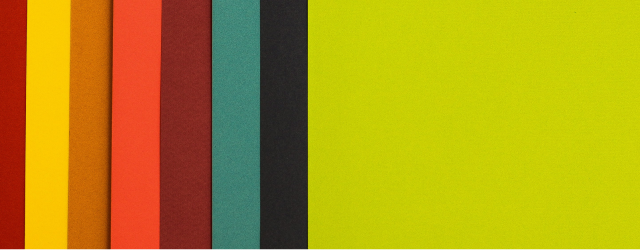
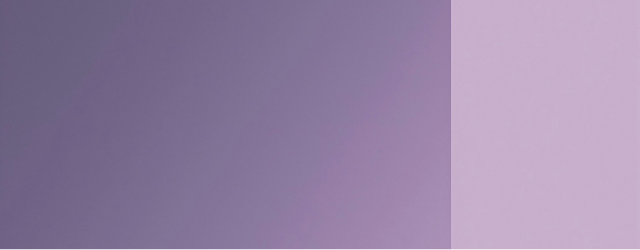
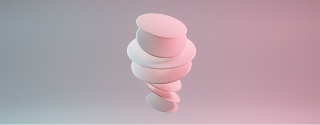
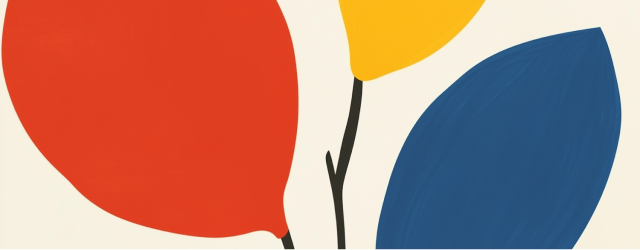
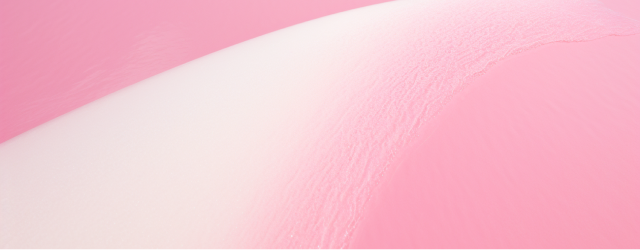
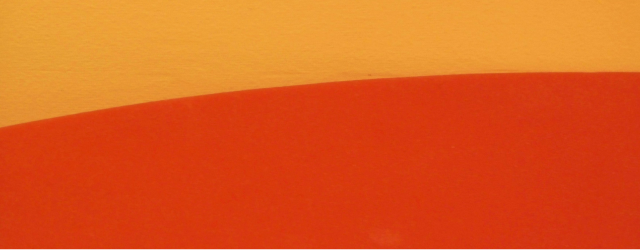