Turnkey Manufacturing
Gain a thorough understanding of Turnkey Manufacturing in manufacturing, with insights into their application, benefits, and strategic importance in the industry.
Overview and Importance of Turnkey Manufacturing
Turnkey Manufacturing refers to a comprehensive production approach where a single provider manages the entire manufacturing process, from initial design to the final product. This concept is significant in today's business landscape as it ensures seamless integration across various production stages, thereby minimizing delays and miscommunications often encountered when using multiple vendors. By adopting this model, businesses can streamline their operations, significantly reducing the time-to-market. For example, in the aerospace industry, companies that utilize turnkey manufacturing can ensure that all components meet strict quality standards while adhering to tight production schedules. The importance of turnkey manufacturing cannot be overstated, as it provides businesses with a strategic advantage by enhancing operational efficiency and ensuring product consistency.
Role in Enhancing Manufacturing Efficiency
The role of turnkey manufacturing in enhancing efficiency is multifaceted. By consolidating production processes, businesses can eliminate redundancies and optimize resource allocation. This approach allows for better coordination and communication throughout the supply chain, resulting in improved product quality and timely deliveries. A notable example is the electronics industry, where rapid product cycles demand swift production adjustments. Turnkey manufacturing enables electronics companies to adapt quickly to design changes without compromising on quality or delivery timelines. Furthermore, this model often leads to cost savings by reducing overheads associated with managing multiple suppliers and production lines. Through strategic partnerships with specialized turnkey providers, businesses gain access to advanced technologies and expertise that further enhance production efficiency and competitiveness.
Navigate Manufacturing Project Success with Meegle
Historical development of turnkey manufacturing
Origins and Early Adoption
The concept of turnkey manufacturing can be traced back to the industrial revolution when businesses began to realize the benefits of streamlined production processes. Initially, it was adopted by industries with complex production needs, such as aerospace and automotive manufacturing. These early adopters recognized that managing the entire production process in-house was resource-intensive and prone to errors. The shift towards turnkey solutions allowed them to focus on core activities while outsourcing manufacturing to specialized providers. For instance, during the mid-20th century, automotive giants like Ford and General Motors started collaborating with turnkey manufacturers to produce critical components, thereby enhancing production efficiency and consistency. This early adoption laid the groundwork for the widespread integration of turnkey manufacturing in various industries today.
Evolution Through Technological Advancements
Over the years, technological advancements have significantly shaped the evolution of turnkey manufacturing. The integration of automation, robotics, and sophisticated software systems has transformed traditional manufacturing practices into highly efficient and scalable operations. These technologies enable turnkey providers to offer solutions that are not only cost-effective but also flexible enough to accommodate rapidly changing market demands. In the electronics sector, for example, the use of computer-aided design (CAD) and manufacturing (CAM) systems has streamlined the production of complex components, reducing errors and enhancing precision. Additionally, advancements in supply chain management software have improved inventory control and procurement processes, further contributing to the efficiency of turnkey solutions. As technology continues to evolve, turnkey manufacturing is poised to become even more integral to modern production strategies.
Click here to read our expertly curated top picks!
Core principles and techniques
Understanding Fundamental Concepts
The fundamental principles of turnkey manufacturing are rooted in comprehensive project management, system integration, and quality assurance. These pillars ensure that the entire production process is managed efficiently and effectively. Project management in turnkey manufacturing involves meticulous planning, execution, and monitoring of all production stages to ensure timely delivery and adherence to quality standards. System integration, on the other hand, focuses on harmonizing various components of the production process to function seamlessly as a single unit. This includes integrating hardware, software, and human resources to optimize productivity. Quality assurance is critical in turnkey manufacturing, as it guarantees that the final product meets all specified requirements and customer expectations. By adhering to these core principles, turnkey manufacturing providers can deliver solutions that are reliable, efficient, and tailored to the specific needs of their clients.
Implementation Techniques and Best Practices
Implementing turnkey manufacturing requires a strategic approach that encompasses several best practices. Firstly, thorough planning is essential to define the scope, objectives, and timelines of the manufacturing project. This involves collaborating with all stakeholders to ensure alignment and clarity on project goals. Secondly, effective execution relies on leveraging advanced technologies and methodologies to optimize production processes. Techniques such as lean manufacturing and Six Sigma can be employed to minimize waste and enhance quality. Additionally, fostering a culture of collaboration and communication among teams is crucial to address any challenges that may arise during the production process. Finally, continuous monitoring and evaluation of the turnkey manufacturing process enable businesses to identify areas for improvement and implement corrective measures. By adhering to these best practices, companies can maximize the benefits of turnkey manufacturing and achieve sustained success in their production endeavors.
Benefits and challenges
Advantages in Production Efficiency and Output
Turnkey manufacturing offers several advantages that contribute to enhanced production efficiency and output. One of the primary benefits is the reduction in lead times, as the entire manufacturing process is managed by a single provider, ensuring seamless coordination and communication. This streamlined approach minimizes delays and accelerates product delivery to market. Moreover, turnkey manufacturing often results in cost savings by optimizing resource allocation and reducing overheads associated with managing multiple suppliers. Another significant advantage is improved product reliability, as turnkey providers adhere to stringent quality standards throughout the production process. By leveraging the expertise and capabilities of specialized turnkey manufacturers, businesses can achieve higher levels of efficiency and output, thereby gaining a competitive edge in their respective industries.
Addressing Potential Limitations
While turnkey manufacturing presents numerous benefits, it also comes with certain challenges and limitations. One potential issue is the dependency on suppliers, as businesses relinquish control over the manufacturing process to external providers. This reliance can lead to disruptions if the turnkey provider encounters operational challenges or fails to meet quality standards. Additionally, the initial setup costs for implementing turnkey manufacturing can be substantial, particularly for small and medium-sized enterprises. To mitigate these challenges, businesses should conduct thorough due diligence when selecting turnkey providers, ensuring they have a proven track record of reliability and quality. Establishing clear communication channels and performance metrics can also help monitor the progress and performance of turnkey providers. By addressing these limitations, companies can fully leverage the benefits of turnkey manufacturing while minimizing potential risks.
Click here to read our expertly curated top picks!
Case studies and real-world applications
Example: automotive industry transformation
Example: automotive industry transformation
In the automotive industry, a leading manufacturer adopted turnkey manufacturing to streamline its production line and enhance vehicle quality. By outsourcing the production of key components to a specialized turnkey provider, the company was able to focus on core activities such as design and marketing. This approach not only reduced production lead times but also improved the consistency and reliability of the final products. The integration of advanced robotics and automation technologies further optimized production efficiency, enabling the manufacturer to meet increasing consumer demand while maintaining high-quality standards. As a result, the company gained a significant competitive edge in the market, solidifying its position as an industry leader.
Example: electronics manufacturing optimization
Example: electronics manufacturing optimization
An electronics firm implemented turnkey manufacturing to optimize its product development cycles and drive innovation. By collaborating with a turnkey provider, the company gained access to cutting-edge technologies and expertise that facilitated the rapid prototyping and production of new electronic devices. This partnership enabled the firm to quickly adapt to changing market trends and consumer preferences, resulting in a steady pipeline of innovative products. Additionally, the use of advanced quality assurance processes ensured that all products met stringent industry standards, further enhancing the company's reputation for reliability and excellence. Through turnkey manufacturing, the firm achieved significant improvements in operational efficiency and product quality, positioning itself as a leader in the electronics sector.
Example: pharmaceutical production enhancement
Example: pharmaceutical production enhancement
A pharmaceutical company adopted turnkey manufacturing to enhance its drug production capabilities and ensure regulatory compliance. By outsourcing the manufacturing process to a specialized provider, the company was able to focus on research and development activities while maintaining stringent quality control standards. The turnkey provider implemented state-of-the-art technologies and methodologies to optimize production processes, resulting in reduced time-to-market for new drugs. Additionally, the integration of advanced quality assurance systems ensured that all products met regulatory requirements, thereby minimizing the risk of non-compliance. This approach not only improved operational efficiency but also enhanced the company's ability to respond to emerging healthcare needs, solidifying its position as a leader in the pharmaceutical industry.
Technological integration and innovations
Current Technologies Supporting Turnkey Manufacturing
Turnkey manufacturing is increasingly supported by a range of advanced technologies that enhance efficiency and precision in production processes. The Internet of Things (IoT) plays a pivotal role by enabling real-time monitoring and data collection across the manufacturing floor, facilitating proactive maintenance and process optimization. Artificial Intelligence (AI) and machine learning algorithms are employed to analyze production data, predict potential bottlenecks, and recommend improvements, ensuring that the manufacturing process remains efficient and adaptable. Robotics and automation technologies further streamline operations by performing repetitive tasks with high precision and speed, reducing the likelihood of human error. Additionally, digital twins—virtual replicas of physical production systems—allow turnkey manufacturers to simulate and test production processes before implementation, identifying potential issues and optimizing workflows. These technologies collectively enhance the capabilities of turnkey manufacturing, enabling businesses to achieve greater efficiency and product quality.
Future Trends and Innovations
The future of turnkey manufacturing is poised for significant advancements, driven by emerging technologies and innovative practices. One of the key trends is the increasing adoption of Industry 4.0 principles, which emphasize the integration of cyber-physical systems and smart technologies in manufacturing processes. This shift towards digitalization will enhance the agility and responsiveness of turnkey manufacturing, allowing businesses to adapt quickly to changing market demands. Another emerging trend is the use of additive manufacturing, or 3D printing, which offers the potential to produce complex components with reduced lead times and material waste. As sustainability becomes a growing concern, turnkey manufacturers are also exploring eco-friendly practices and materials to minimize environmental impact. Furthermore, advancements in blockchain technology are expected to improve transparency and traceability in supply chains, addressing concerns related to quality control and supplier accountability. By embracing these future trends and innovations, turnkey manufacturing will continue to evolve and deliver even greater value to businesses.
Click here to read our expertly curated top picks!
Tips: do's and don'ts
Do's | Don'ts |
---|---|
Conduct thorough needs assessment | Skip the initial planning phase |
Choose experienced partners | Compromise on quality for cost |
Invest in technology integration | Ignore employee training needs |
Establish clear communication channels | Overlook stakeholder involvement |
Monitor and evaluate performance regularly | Neglect continuous improvement |
Click here to read our expertly curated top picks!
Faqs about turnkey manufacturing
What is Turnkey Manufacturing?
Turnkey Manufacturing is a comprehensive production approach where a single provider manages the entire manufacturing process, from design through to the finished product. This model is designed to streamline operations by integrating all aspects of production under one roof, ensuring efficiency, quality, and timely delivery. A common misconception is that turnkey solutions are inflexible; however, they can be tailored to meet the specific needs and objectives of different businesses.
How does Turnkey Manufacturing enhance efficiency?
Turnkey Manufacturing enhances efficiency by consolidating all production activities, which reduces redundancies and optimizes resource allocation. This approach allows for better coordination and communication across the supply chain, minimizing delays and ensuring timely delivery of products. By leveraging advanced technologies and methodologies, turnkey manufacturing providers can also improve product quality and reduce production costs, contributing to overall operational efficiency.
What industries benefit most from Turnkey Manufacturing?
Turnkey Manufacturing is beneficial across various industries, particularly those with complex production needs or rapidly changing market demands. Industries such as automotive, electronics, aerospace, and pharmaceuticals have embraced turnkey manufacturing to optimize their production processes, enhance product quality, and reduce time-to-market. By adopting turnkey solutions, these industries can focus on their core competencies while leveraging the expertise and capabilities of specialized providers.
What are the common challenges in implementing Turnkey Manufacturing?
Implementing Turnkey Manufacturing can present several challenges, including dependency on suppliers, initial setup costs, and potential disruptions due to operational issues within the turnkey provider. To overcome these challenges, businesses should conduct thorough due diligence when selecting partners, establish clear communication channels and performance metrics, and regularly monitor and evaluate the turnkey manufacturing process to identify areas for improvement.
How is technology transforming Turnkey Manufacturing?
Technology is playing a crucial role in transforming Turnkey Manufacturing by enhancing efficiency, precision, and adaptability. The integration of IoT, AI, robotics, and digital twins enables real-time monitoring, data analysis, and process optimization, leading to improved production outcomes. As technology continues to evolve, turnkey manufacturing is becoming more agile and responsive, allowing businesses to quickly adapt to changing market demands and achieve greater competitive advantage.
Conclusion
Recap of Key Insights
In conclusion, Turnkey Manufacturing has emerged as a powerful strategy for modern industries seeking to enhance efficiency, reduce time-to-market, and ensure high-quality production. By consolidating all aspects of manufacturing under a single provider, businesses can streamline operations, optimize resource allocation, and focus on their core competencies. The benefits of turnkey manufacturing include reduced lead times, cost savings, and improved product reliability, which collectively contribute to a competitive edge in the market. However, companies must be mindful of potential challenges, such as dependency on suppliers and initial setup costs, and implement strategies to mitigate these risks.
Encouraging Ongoing Innovation and Adaptation
As the industrial landscape continues to evolve, it is crucial for businesses to stay informed about ongoing developments in Turnkey Manufacturing and consider its integration into their operations. By embracing emerging technologies and innovative practices, companies can ensure sustained competitive advantage and adaptability in a rapidly changing market. As turnkey manufacturing continues to evolve, it will undoubtedly play an increasingly vital role in shaping the future of production and industry as a whole.
Navigate Manufacturing Project Success with Meegle
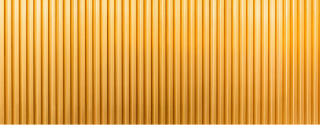
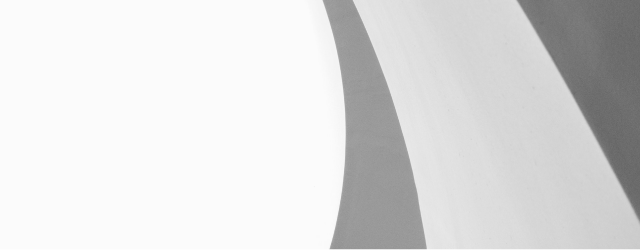
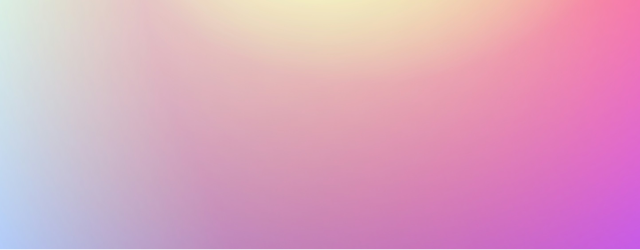
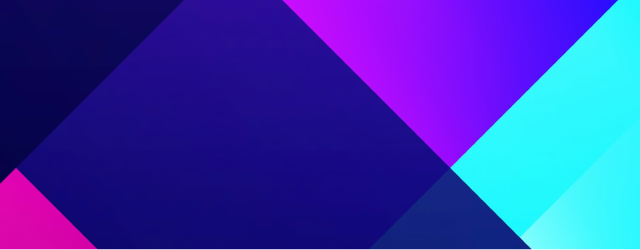
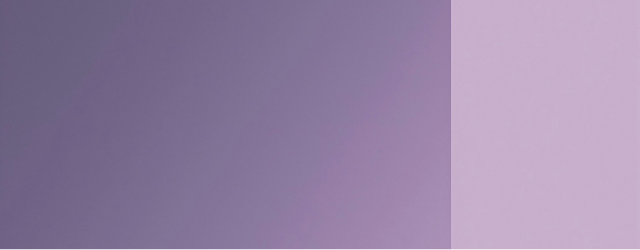
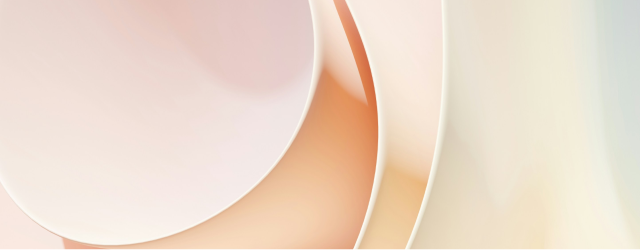
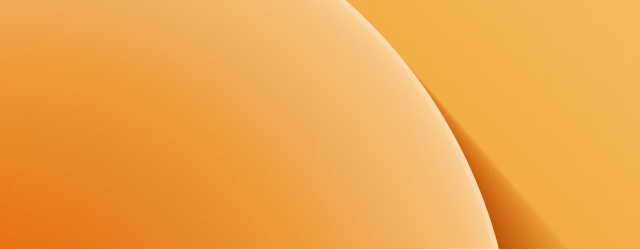
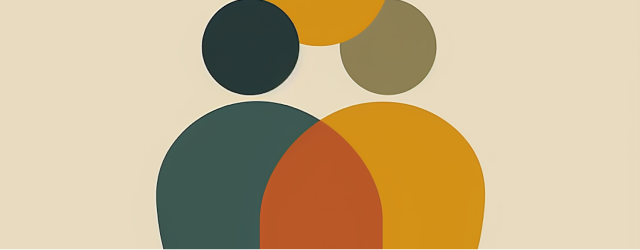